Constructing a house or a commercial building with a unique design within a strict deadline is a challenge, and homeowners often have to sacrifice either time or design. However, spray-on concrete or shotcrete has been a revolutionary method, providing a balance between the two.
They offer numerous benefits in the construction industry and have been used for a wide range of applications in residential and commercial buildings. This blog will explore spray-on concrete in detail and will help you gain a deeper understanding of how it is done.
What is Spray-on Concrete?
Spray-on concrete or shotcrete is a method of applying concrete to surfaces by spraying it through the nozzle under high pressure. This application can be used for a wide range of applications, including vertical, horizontal, and overhead structures directly without the need for formwork. The shotcrete used is of two types— dry-mix shotcrete and wet-mix shotcrete, and the application process and equipment differ based on the type.
Planning and Design
Accessing Project Requirements
It is necessary to identify the specific needs of the project, whether to construct structural reinforcement, decorative elements, or pool construction for other parts of the structure. After understanding the need, the type of concrete mix must be determined along with the necessary additives.
Ensure that the design possesses the required load-bearing capacity, resistance to external conditions, and durability to withstand the elements for a long time. Set up an appropriate estimate and timeline based on the complexity and scope of the work.
Design Specifications
After understanding the requirements, create a design for the structure’s shape, determine the reinforcements, and specify the types of finishes to get a clear view of the structure that needs to be built with sprayed concrete.
Site Preparation
Surface Cleaning
Prepare the surface over which the structure needs to be installed. Ensure that the surface is free from dust, oil, grease, or contaminants on the existing concrete. Any cracks or voids formed on the surface need to be addressed, as they could affect the bonding.
Moistening the Surface
After cleaning, use light moisture on the surface to improve adhesion and prevent rapid evaporation caused by shotcrete, to ensure proper curing and water seepage.
Equipment Setup
Selection of Equipment
- The use of shotcrete machines varies based on the type of shotcrete materials used. Choose either a dry-mix or wet-mix shotcrete machine.
- Air compressors are essential for dry-mix shotcrete to propel the concrete into the nozzle.
- Pumps are used for wet-mix shotcrete to push the mixed concrete into the hose.
- Nozzles and hoses allow the control and flow of shotcrete in the spray pattern.
Safety Checks
Ensure that all the machines and equipment are in working condition to maintain an efficient flow, without causing any blockages or leakages.
Application Process
Nozzle Technique
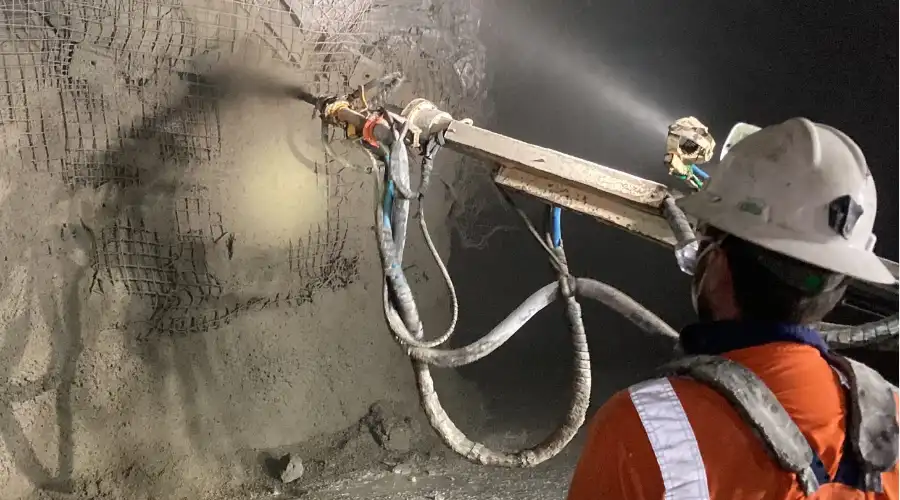
Keep the nozzle at an appropriate angle between 30° and 90°, and spray at a distance of 45 cm to 90 cm for even distribution of shotcrete. The spraying process needs to be carried out back and forth, ensuring a uniform and consistent layer thickness.
Layering

If the surface is rough or porous, spray the first layer of shotcrete in a thin layer to create a tight bond with the substrate. After the initial layering, fill the subsequent layer with a thickness of 1 to 2 inches, with frequent intervals, allowing time to set until it achieves the desired thickness.
Finishing
Surface Finishing
After the shotcrete is completely applied, finishing tools such as trowels, floats, or brushes can be used to achieve the required texture.
Curing
After application, keep the shotcrete structure moist for at least a week to allow the structure to attain the necessary strength and hydration. Periodic sprinkling of water can be done to keep the surface wet.
In the case of rapid direct drying, avoid the exposure of structure to direct sunlight or hot external temperatures, as they could cause cracks in the surface.
Quality Control
Testing
The wet-mix shotcrete can be tested in the laboratory using a slump test to measure the workability. Compressive tests can be done to ensure the load-bearing capacity of the shotcrete after 7 and 28 days of curing. In the construction of tunnels and pools, the bond strength of the shotcrete to its substrate is tested.
Inspection
Visual inspection of the shotcrete surface can be done to ensure consistency in application, evenness in layering, and to check for cracks, defects, and honeycombing caused by poor compaction.
Safety Considerations
- It is mandatory to ensure that all the workers wear safety gear and are equipped with safety glasses, gloves, face shields, and hearing protection among other safety measures.
- In dry-mix shotcrete, there is a risk of dust pollution through the air; thus water sprays and proper ventilation methods can be used to suppress it.
- Site safety must be ensured by establishing emergency protocols in case of accidents and keeping the non-workers at a safe distance to prevent injuries.
Conclusion
In summary, spray-on concrete or shotcrete is an advanced and efficient method that is used in various construction applications. It offers a wide range of benefits in design flexibility and speed of construction. However, there are certain challenges when it comes to labour costs, equipment costs, and environmental concerns. But when carefully carried out, it can deliver superior results.
FAQs
Dry mix shotcrete is typically used for highly flexible and precise projects, such as for repairs and artistic features, where minute details are crucial. On the other hand, wet-mix is suitable for large and robust projects, where strength and durability are crucial.
Yes, shotcrete or spray-on concrete can be applied to all types of vertical, horizontal, and overhead surfaces and can be highly effective.
Some of the common issues associated with spray-on concrete are,
1. Inconsistent bonding- This can be avoided by proper surface preparation
2. Uneven or rough finish- This can be avoided by applying from an appropriate distance and through experienced labour.
3. Cracking- It can be prevented by applying concrete in thin layers, using reinforcements, and following a controlled curing process.
4. Sagging- This can be avoided by proper mixing of shotcrete and using the right equipment.