Are you in charge of a high-rise project or extensive commercial build and finding that a common timber formwork just isn’t fitting into your program and durability requirements? You are not alone. Many contractors and project managers alike have dealt with delays and increasing costs due to the numerous repairs and replacement of wood shuttering panels. Let’s introduce you to steel shuttering—a durable, reusable type of formwork that is quickly becoming the preferable option for larger projects. In this article we’ll guide you on everything you need to know about steel shuttering, starting from its definition to practical tips on care and maintenance. If you’re interested in streamlining your workflow, Brick & Bolt offers custom steel formwork solutions that can save time and money on your next project.
What Is Steel Shuttering?
Steel shuttering, or steel formwork, is a system of prefabricated panels, props and accessories that are primarily made from high-quality steel and used to create a mould that concrete is poured into. It enables concrete to obtain a specific shape and gain strength as it cures. Unlike wood or plywood shuttering which will warp, splinter and degrade over a number of uses, steel shuttering will provide a much higher reusability rate. Ensuring uniformity in the dimensions of the panels and finish of the concrete, steel shuttering is ideal for making flat slabs, columns, curved walls, beams and other concrete components.
Benefits of Steel Shuttering
- Durability and Longevity: Steel panels can endure extreme conditions on site, whether it be rain, chemicals, UV exposure, or rough handling, without compromising their structural integrity. You can typically expect to get 200+ uses from each panel, while plywood will typically give you about 25-30.
- Increased Cycle Times: Since steel shuttering fittings are manufactured to ensure quick assembly and dismantling, you can decrease your formwork cycle time by as much as 20%. With faster disassembly and reassembly, you can improve your construction schedule.
- Superior Concrete Finish: The non-porous, smooth surface of steel provides a quality finish that minimises the amount of patching & plastering required for concrete. This not only saves on labour, but helps projects get completed sooner.
- Cost-Effectiveness: While steel formwork will cost more initially, the low maintenance & high reusability will lower the overall cost per unit area of formwork. This can result in significant savings on long term or large construction projects.
- Safety and Stability: Steel props and bracing systems have a higher load bearing capacity and limit the deflection under loads, thereby providing a safer workplace for your crew.
Types of Steel Shuttering Used in Construction
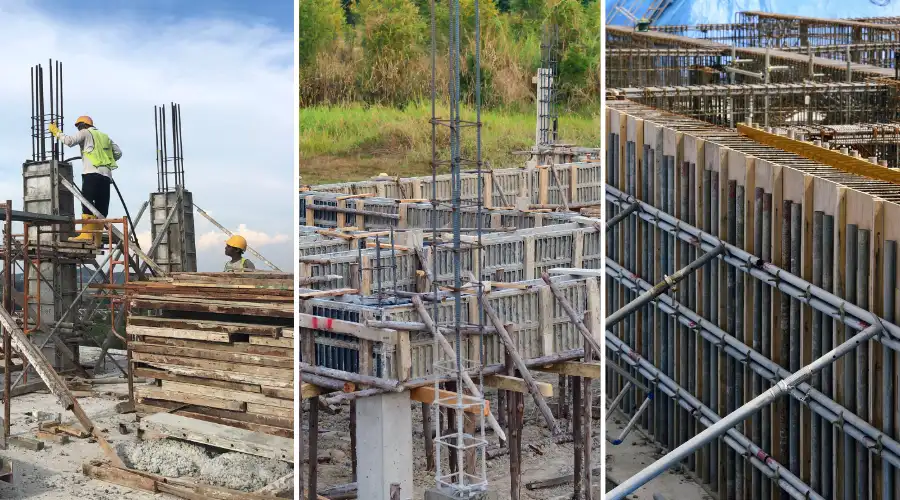
- Panel Formwork: This includes flat, modular panels that assemble into walls, slabs, footings and other similar surfaces. Panels are usually available in standardised sizes and interconnected using simple wedge or clamp systems, and other options depending on the manufacturer.
- Column/ Beam Formwork: More commonly known as column forms, these hinged or bolted systems can be used for columns with different cross sections like square, rectangular, or circular. Round column formwork generally has easily adjustable ties to expand or contract for different diameters.
- Curved Formwork: Made expressly for curved forms. They have flexible, specialised steel sheets that can be bent to any specified radii. Such formwork is commonly used to make circular tanks, tunnels, and decorative architectural elements.
Steel formwork can also be customised to suit specific requirements of shape and form. However, this is often more expensive.
Applications of Steel Shuttering in the Construction Industry
- High-Rise Construction: Steel formwork excels with repetition and consistency. From core walls to slabs, this method allows for each pour to be constructed to the same dimensions, and reduces cumulative dimension errors, which is especially important for high-rise structures with repetitive forms on each floor.
- Industrial Structures: When it comes to speed and strength, steel shuttering is an asset to factories, warehouses, and power plants. This system efficiently handles heavy pours and close tolerances in a very controlled process.
- Bridges & Infrastructure: For bridges, piers, deck slabs, abutments and other large infrastructure projects, fast cycle times, strict project timelines and high load-bearing needs can be fulfilled with steel shuttering.
- Tunnels & Stacks: Curved or cylindrical formwork for vertical structures is a great way to utilise modular steel sections that clamp together to form one continuous, leak-proof, and pump-proof mould to pour concrete.
- Water Retaining Structures: Dams, reservoirs, and swimming pools all require concrete surfaces to be watertight. The precision provided by the steel shutters minimises the chances of leakage, while efficiently producing the smooth finishes required to retain liquids.
Factors to Consider When Choosing Steel Shuttering
- Project Size and Site Conditions: Large, reusable pours justify the up-front cost of steel. Conversely, for smaller, one-off jobs, it may make economic sense to use a hybrid system which integrates plywood instead of steel into the formwork system.
- Concrete Pressure and Pour Height: The greater the pour weight or height, the higher the lateral pressure the formwork will generate. Use a panel and tie that has a rating to handle the hydrostatic pressure you will likely create with the pour weight. Otherwise, you risk bulging and blowouts.
- Panel Size and Weight: The larger the panel, the more efficient the assembly. However, for large panels you will need cranes or other lifting equipment. Factor in the available equipment and site logistics to find the best panel sizes.
- Accessories and Compatibility: Check whether different props, ties, and clamps are compatible across the formwork system. It is best practice to standardise your formwork systems as much as possible to minimise the potential of incompatible parts and downtime.
- Budget and Life-Cycle Cost: Consider the total cost of ownership, including purchase cost, expected cycles of reuse, maintenance, and disposal value at the end of the project. The resale or return-deposit value of steel can recover part of your investment.
How is Steel Shuttering Made?
- Design and Engineering: First, shop drawings are created, which include specifications of panel size, tie locations, and accessory layouts. Modern computer-aided design software is often used to ensure that the design is closely aligned with the structural plans.
- Panel Fabrication: High-grade structural steel sheets are cut and roll-formed to specified dimensions. Edges are flanged, and any chamfers are pre-set so that the desired concrete edge profile can be attained.
- Welding and Assembly: Welders will assemble and weld flanges, stiffeners, and connection brackets in accordance with the standards of the chosen industry body (e.g., IS 4661 or equivalent). A quality inspection is performed to verify the weld integrity and that the panels are being manufactured correctly in terms of dimensions.
- Surface Treatment: Panels will receive a corrosion resistant surface finish— such as epoxy coating or galvanisation—to extend service life and maintain smoothness for concrete pouring.
- Accessory Fabrication: Props, walers, tie rods and clamps should be machined or forged to specified sizes. A mechanical load test is completed for all accessories that would experience typical loading conditions on-site.
- Quality Inspection & Certification: Each batch of panels and accessories are inspected to verify the steel grade, coating thickness, flatness, and connection fit. A certificate of conformity supports traceability and compliance with the safety guidelines.
Maintenance and Care of Steel Shuttering
- Regularly Clean: Every time you use your panel and pour concrete, you should thoroughly remove every residue of hardening concrete with water and a soft brush. This ensures that honeycombs, cracks and other such issues in concrete do not occur when the shuttering is used again. Do not use any abrasives that might scratch or otherwise damage the coating.
- Apply Release Agent: Each time you use your panel you need to spray or brush a very thin layer of formwork oil on it to make it easier to remove the formwork and stop concrete from adhering to the panel.
- Check for Damage: Make sure you look for deformations, cracks and worn threads on the panels and accessories every time you use them. Once you identify any damaged items, either fix or replace them to retain safety and smooth finishes.
- Properly Store: Panels need to be stored flat, off the ground, under cover to prevent corrosion. Do not store your wooden and steel formwork together as moisture can be transferred.
- Set a Program of Refurbishment: Most panels should be refurbished after approximately 100-150 uses. Work with your formwork supplier to determine how they can provide on-site refurbishment services in your area.
Conclusion
Steel shuttering has revolutionised modern construction, offering an unrivaled combination of durability, accuracy, and cost savings- something that traditional timber formwork cannot offer on a large scale. Whether you are dealing with high-rise structures, bridge decks or curved architectural elements, a thoughtfully designed steel formwork system will speed up your schedule, improve the quality of your concrete and decrease costs in the long run. Interested in optimising your next project? Brick & Bolt offers end-to-end steel shuttering support all the way to the job site. We mobilize the design, fabrication, onsite support and ongoing maintenance to ensure your projects are built to last, on time and within budget. Let’s build smarter together!