Gauged mortar is a mixture of lime and cement as the main materials for binding. Such a mix will optimize the workability of lime and the stability of cement, thus making it suitable for different masonry and plastering tasks. The introduction of gauged mortar has become a common trend in contemporary construction, offering ease of work, rapid setting, and thereby enhancing bonding and durability. Additionally, it is a factor in achieving better finish quality and cost-effectiveness in both load bearing walls and non-load-bearing walls.
What is Gauged Mortar?
Gauged mortar, also known as lime-cement mortar, is made by mixing cement, lime, fine sand, and water in specific proportions. It has been designed to overcome the drawbacks of using mortar of only one type, either lime mortar or cement mortar. “Gauging” is the process of adding the right amount of lime to cement in order to obtain the necessary chemical and physical characteristics. As a rule of thumb, lime is mostly plastic and flexible, whereas cement has fast-setting and high strength. The usual ratio according to the construction standard varies from 1:6 to 1:9 (cement:lime), depending on the design requirements.
Benefits of Gauged Mortar
- Improved Workability: The inclusion of lime in the mortar mix provides superior workability characteristics, making it more cohesive and easier to spread. This property also ensures that the physical effort required during the construction process is reduced, resulting in a more uniform bedding of masonry units.
- Cost Efficiency: Lime is considerably cheaper than cement. The use of lime in place of some of the cement in the mortar mix results in a substantial decrease in the total cost of the mortar. In this way, it becomes practical to use gauge mortar in such large-scale construction projects without compromising the required quality.
- Enhanced Bond Strength: Lime’s plasticity feature ensures the mortar fills the voids excellently and closely associates with the brick or block surface. Consequently, this forms a tighter connection between the units, which in turn, leads to the walls being stronger and more stable structurally.
- Shrinkage Reduction: To illustrate, experience with cement mortars indicates that shrinkage cracks can easily occur once they begin to dry. The inclusion of lime in gauge mortar solves the issue of shrinkage and cracking by increasing the mortar’s elasticity.
- Longer Open Time: The presence of lime in gauged mortar slows down the initial setting time, allowing the mortar to remain workable for a longer duration. This extended open time gives masons greater flexibility to apply the material efficiently, especially during complex or large-scale work. It helps improve the ease of application and provides better timing control during construction.
- Improved Water Retention: The plasticization provided by lime makes the mortar much water-resistant than pure cement mortar. This helps in maintaining adequate moisture levels during curing, which is essential for strength development and durability.
- Better Bond Strength: The combination of cement and lime in gauge mortar helps achieve good adhesion between masonry units.
Purpose of Gauging in Mortar
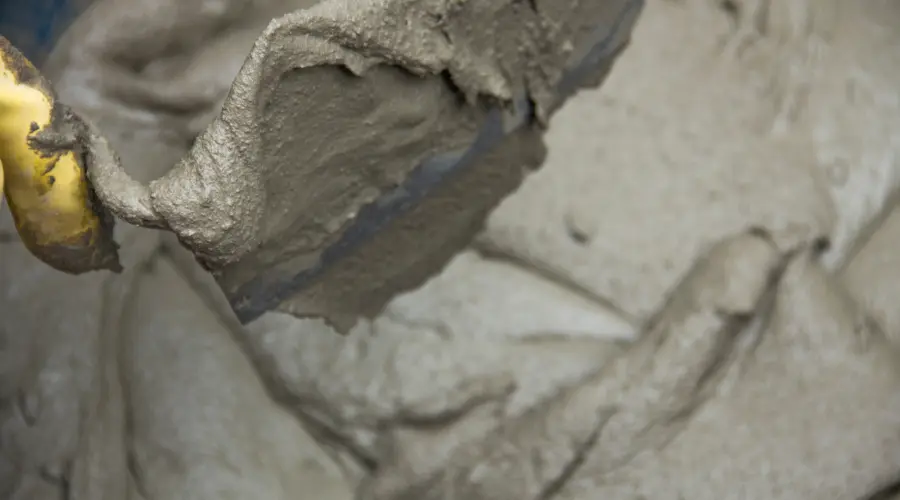
- Gauging is performed to make minimal adjustments to the nature and properties of mortar, ensuring it is completely suitable for the site. Among other things, its functions are:
- Adjusting Setting Time: Cement speeds up the setting that naturally occurs in the mortar mixture, while lime has the opposite effect. Gauging the mix ensures a suitable setting, making it possible to do everything without difficulties and at the same time allowing an extended variant of working in the case of complex applications.
- Combining Strength and Flexibility: In the case of structural application, the strength of a certain level is an essential requirement, which is facilitated by cement. Lime, in turn, minimizes the hardening effect and introduces greater resilience, thus forming a crack resistance and stress capacity that guarantees the long-lasting use of concrete conservatories.
- Improving Finish Quality: The finer lime particles in the finish make and enable a luster surface when plaster or mortar is treated smoothly. This is particularly important during the final stages of construction, where surface uniformity and aesthetic appeal are crucial, requiring skilled craftsmanship and quality materials.
- Compatibility with Heritage Structures: Gauged mortars are ideal for restoring historical buildings, as they closely replicate traditional lime mortars used in original construction. This makes them well-suited for projects where preserving the appearance, texture, and integrity of heritage structures is essential.
Applications of Gauged Mortar
- Masonry Construction: In masonry construction, the use of gauged mortar is the norm, especially, in the building of brick and block masonry where moderate strength and high workability are relevant. It is flexible in such a way as to accommodate minor movements in wall panels avoiding vibration crack formation.
- Plastering Works: The smooth and workable nature of gauged mortar makes it ideal for plastering both internal and external surfaces. It provides a refined finish with fewer cracks and better adherence to wall substrates.
- Restoration Projects: Heritage and conservation projects require materials that are compatible with traditional lime mortars. Gauged mortar is widely used in such contexts for pointing and rendering to maintain historical authenticity while improving performance.
- Low to Medium Rise Buildings: In residential buildings, schools, and small commercial structures, gauged mortar offers a practical solution due to its affordability and sufficient strength for non-critical applications.
- Partition Walls and Non-Load Bearing Units: These applications benefit from the elasticity and light weight of gauged mortar. It offers ease of application, quicker set time compared to pure lime mortars, and a smooth finish for interior surfaces.
Composition of Gauged Mortar
The composition of gauged mortar includes the following components:
- Cement: Typically Ordinary Portland Cement (OPC), used for achieving early strength. It ensures the mortar attains the required compressive strength within the stipulated time.
- Lime: Either fat lime or hydrated lime (Type S), added to increase workability and plasticity. Lime improves bonding and accommodates thermal movements in masonry.
- Sand: Clean, well-graded sand with minimal silt content is used as a filler material. Sand provides volume, reduces shrinkage, and supports the development of a strong matrix.
- Water: Potable water should be used. Water content must be precisely controlled to ensure proper hydration of cement and activation of lime, achieving desired consistency.
Standard Mix Ratios:
The standard mix ratio of cement to lime varies from 1:6 to 1:9.
It is advisable to use mechanical mixers for achieving an even mixture of binders and aggregates. Moreover, the practice of batch measurements and the consistent procedure of mixing will greatly enhance the uniformity and performance of the mortars.
Application Process of Gauged Mortar
- Surface Preparation: Prior to the application of mortar, ensure that the masonry units are clear and slightly wet but not soaking. Damp surfaces can absorb the water of the mix, causing poor bond or low strength.
- Mixing Process: Lime should first be mixed with water to form a lime putty, especially if using fat lime. Cement and sand are dry mixed separately, and then the lime putty is gradually added to this mixture. Water is then added in small quantities until the desired workable consistency is achieved. The entire mix should be blended thoroughly using a mechanical mixer for at least 5–10 minutes to ensure uniformity and homogeneity..
- Application Method: For masonry construction, the mortar is efficiently applied to both the base and the vertical joints. The thickness is equal throughout, usually 10-12mm. On the other hand, in plastering, a trowel is used to apply the mortar to the wall and then it is pressed well against the wall surface.
- Finishing: Depending on the finish you want, you can use a wooden float or steel trowel to carry out the job. Before finishing, smooth out the surface to remove any bumps. Alternatively, before doing the final finish, it is good to let the cement harden slightly.
- Curing: Curing should begin as soon as the mortar has set sufficiently, usually 24 hours after application. After this initial period, moist curing should be continued for a minimum of 7 days, particularly in hot and dry conditions. The curing process prevents the mortar from drying too quickly, allows for proper hydration, and ensures optimal strength and adhesion of the mortar. Consistent moisture during curing significantly enhances the long-term durability and bonding capacity of the mortar.
Conclusion
Gauged mortar is a crucial construction material that preserves the traditional dynamics while also introducing a modern dimension of performance. As it involves the combination of lime and cement, it becomes the choice for workability, economy, and strength. Through its various applications, ranging from masonry and plastering to heritage restoration, gauged mortar can be considered highly adaptable. Properly mixed, gauged mortar is not only able to make masonry structures more durable, but it can also significantly improve their aesthetics.