Concrete is the building material of today. It’s in skyscrapers, sidewalks, and everything in between. Practically every building worker is aware that it’s tough to achieve the right consistency, strength, and durability in concrete. It needs to add too much water to make it workable, though, which robs the mix of strength. Concrete plasticizers are called in here. Concrete plasticizers allow concrete to be made workable without compromising its integrity.
In this blog, we’ll explore plasticizers, how they work, the types available, and how to choose the right one for your project.
The Basics of Concrete Plasticizer
Plasticizer is an admixture used in concrete that enhances its workability by lowering the water content required to attain a specific consistency. In a manner that lowers the water-cement ratio merely moderately, plasticizers enhance the flow and placeability of the mix, its compactness, and finish. This flowability is enhanced without decreasing the strength or toughness of the concrete.
Plasticizers are particularly valuable in mixes where minimum water-cement ratios are required, like in heavy structural elements and high-performance concrete. Plasticizers improve the cement particle dispersion, achieving improved bonding and void reduction, and thus stronger and more resistant concrete.
Generally, 1-2% plasticizer for each unit of concrete weight will produce the desired effect. One has to be prudent not to add too much because it would make the concrete separate or get weakened.
How Concrete Plasticizers Work
Plasticizers make concrete workable by dispersing cement particles through electrostatic or steric forces, depending on the chemical nature of the admixture. These surfactants also adsorb onto cement particles and form ionic groups projecting out. This imparts a negative charge to the particles so that they electrostatically repel one another. The originally flocculated or agglomerated cement grains are therefore separated, and there is more dispersion in the mix.
Creation of an oriented film of water molecules over every cement particle also aids such segregation. Such a film of water inhibits agglomeration of particles, and thus the flow and lubrication of the mix are improved.
Thus, water earlier trapped in flocculated structures becomes free, adding significantly to workability. Paste softens and becomes fluid, reducing internal friction and, once more, improving fresh concrete performance.
Types of Plasticizer Used in Concrete Mix
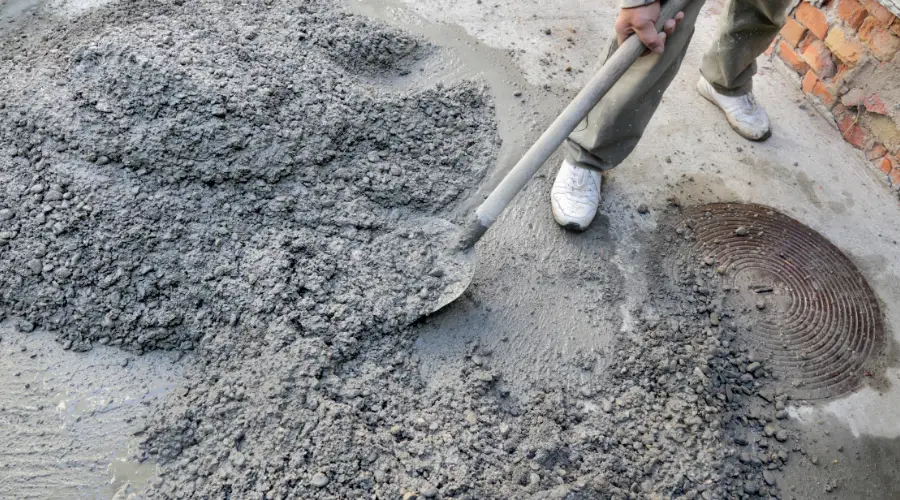
Generally, concrete plasticizers are classified into two categories as follows.
1. Hydrophilic plasticizers are workability- and flow-enhancing combinations that increase the wetting capability of cement.
2. Hydrophobizing plasticizers let more air get into the concrete mix. It also helps reduce the tension between water molecules. It makes the concrete easier to mix and shape.
Purpose of Using Plasticizer
- Improve workability without increasing water content.
- Reduce water-cement ratio while maintaining desired consistency.
- Enhance the strength and durability of hardened concrete.
- Facilitate better placement and compaction, especially in congested reinforcement.
- Reduce internal friction among concrete particles for smoother flow.
- Prevent segregation and bleeding, leading to a more cohesive mix.
- Improve surface finish and reduce honeycombing in formwork.
- Help in producing high-performance or self-compacting concrete (SCC).
- Allow efficient concrete pumping, especially in tall or complex structures.
The Benefits of Concrete Plasticizer
Plasticizers have several practical benefits in concrete construction.
- Increased Strength: Lower water content results in a denser concrete mix, improving compressive strength and overall performance.
- Improved Workability: Plasticizers enhance the flow and ease of placing concrete without adding extra water. This makes the mix more workable, especially in congested reinforcement areas.
- Reduced Water-Cement Ratio: They allow a reduction in water content, leading to higher strength and better durability without compromising workability.
- Enhanced Durability: By minimizing water usage and pore formation, plasticizers help produce less permeable concrete, increasing resistance to weathering, sulfate attack, and corrosion.
- Better Surface Finish: Improved flow leads to smoother finishes with fewer honeycombs or surface defects, reducing the need for extensive surface repair.
Compounds of Concrete Plasticizer
Concrete plasticizers are manufactured from several different chemical compounds with various advantages.
Lignosulfonates and Their Derivatives
Lignosulfonates are sulfonated hydrocarbon salts and are among the oldest and most common plasticisers. They help lower the water content in the mixture and improve its flowability, making them especially suitable for use in large-scale concrete applications. Modified lignosulfates enhance setting time and reduce segregation.
Carbohydrate-Based Plasticizers
They are sustainable materials usually derived from starches and sugars. They are incorporated into concrete mixtures in minimal quantities, typically ranging from 0.1% to 0.4% of the total cement mass. Despite a small amount, they make a big contribution. At the same time, they save 5% to 15% of water demand, which improves strength naturally.
They have the ability to raise the slump by 30 to 150 mm while maintaining the same water-to-cement ratio, depending on factors such as the cement type, initial slump level, and the amount of plasticizer used.
Factors to Choose the Right Concrete Plasticizer
Selecting the appropriate plasticizer for concrete depends on the particular needs. Begin by determining whether you require improved workability, reduced water content in the mix, or increased setting time. A normal plasticizer can be employed for normal construction, but for high-strength or low water-cement ratio mixes, a high-range plasticizer would be the best.
Consult Specialists
Get advice from concrete specialists, for example, engineers, contractors, or suppliers. They possess rich experience and knowledge of concrete plasticizers and can guide you based on your project needs. They will assist you in choosing a plasticizer suitable for your needs and provide the best results.
Look at Performance Data
Check the technical data and performance characteristics given by the manufacturers. Check for workability, setting time, strength gain, and unique benefits or limitations of the plasticizer. Comparison of various manufacturers’ data will provide you with an idea of what each product has to offer and help you make a proper choice.
Consider Environmental Aspects
Take into consideration the environmental conditions in which the concrete will be cast. Temperature, humidity, and exposure to chemicals or harsh weather conditions may impact the plasticizer’s performance. Employ a plasticizer that is compatible with the specific environmental conditions of your project to provide long-lasting performance and durability.
The End Line
Concrete plasticizers are now a necessity in modern construction, offering a brilliant solution to improving fresh and hardened concrete characteristics. Through the reduction of water needed while maintaining or enhancing workability, plasticizers allow stronger, more resistant, and more cohesive mixes to be achieved.
They are particularly valuable for money in obtaining high-performance concrete, free-flowing mixes, and increased surface finishing with no loss of structural integrity. Plasticizers are an essential component of the concrete mix when each project requires a low water-cement ratio, high strength, and sound workability.