Ever walked into a building and wondered if those columns can handle the load? Or maybe you’re a contractor dealing with aging structures that need beefing up without breaking the bank? You’re not alone.
Structural integrity problems have caused significant pain for property owners – from residential homeowners who find cracks in their basement columns, to commercial developers who want to upgrade their buildings for heavier equipment or machinery. The good news is that not every problem requires you to demolish everything and start new.
For engineers and contractors, concrete jacketing has emerged as the preferred choice for quickly and economically strengthening structures without a complete demolition when needed. It’s like giving your building’s skeleton a serious revamp.
What is Concrete Jacketing?
Think of concrete jacketing as encasing your existing concrete members in a protective sleeve. You are effectively wrapping columns, beams, or foundations with new reinforced cement concrete to create a stronger, composite member that can support heavier loads than the original member.
The beauty of this method is that you aren’t replacing anything. You are strengthening the existing member by bringing it up to a new level of performance. Many contractors like this solution because it enables the project to move forward and avoid the costs associated with large-scale demolitions.
Scope of Concrete Jacketing
- Fixing Structural Weaknesses
Jacketing works wonders for columns showing signs of distress – whether it’s concrete spalling, rebar corrosion, or simply being undersized for current loads. Many older buildings were built to different codes, and jacketing brings them up to modern standards without major reconstruction.
- Earthquake Retrofitting Projects
In seismic zones, jacketing is a lifesaver in getting buildings to current life-safety performance levels. Working with existing members to add ductility and strength is far more cost-effective than replacing them altogether. This makes the overall structure much safer during ground movement.
- Building Upgrades and Expansions
When clients want to add floors, install heavy equipment, or change building use, jacketing often provides the extra capacity needed. It’s particularly useful for warehouse-to-office conversions or adding manufacturing equipment to existing structures.
- Emergency Repairs After Damage
After fires, floods, or other disasters, jacketing can help restore and even improve a structure’s capacity. It’s faster than replacement and often more economical for insurance claims and quick sustainable renovation techniques for existing buildings.
Pros and Cons of Concrete Jacketing
Pros of Concrete Jacketing
- Budget-Friendly Solution
Jacketing typically costs 30-40% of what you’d spend on complete member replacement. For contractors, this means competitive bidding and satisfied clients who don’t have to blow their construction budgets.
- Serious Strength Gains
It can double or triple the load capacity in many cases. A 12-inch column can become equivalent to an 18-inch column with proper jacketing design.
- Minimal Downtime
Unlike full reconstruction, jacketing can often be done while buildings stay occupied. This is huge for commercial properties that can’t afford extended closures.
- Long-Term Durability
When done correctly, jacketing can last for decades. It’s not a band-aid fix – it’s a permanent upgrade that adds real value to properties.
Cons of Concrete Jacketing
- Space Constraints
Jacketing makes members larger, which can consume room dimensions. In tight spaces, this might affect architectural plans or mechanical systems.
- Skilled Labor Requirements
This isn’t basic concrete work. You need experienced and skilled labour who understand composite action, proper surface prep, and reinforcement detailing.
- Construction Timeline
Proper curing and phased construction can extend project schedules. Weather delays and multi-stage work sequences add complexity to project planning.
- Existing Condition Dependencies
Severely deteriorated concrete might need extensive prep work or may not be suitable for jacketing at all. Sometimes replacement is the only viable option.
Types of Concrete Jacketing
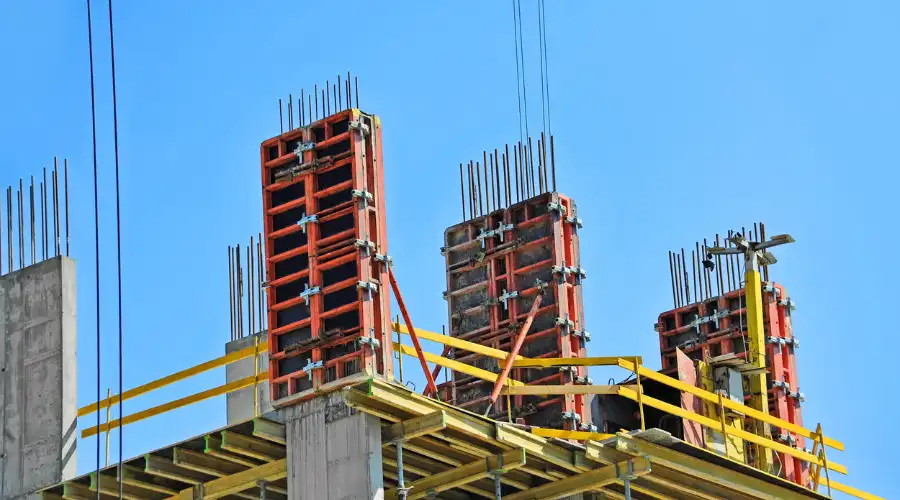
Concrete jacketing methods vary based on the structural needs, space availability, cost considerations, and target performance improvements. Choosing the right type depends on the structure’s existing condition, load demands, seismic vulnerability, and operational limitations. Each technique has unique advantages and best-use scenarios, especially in retrofitting projects, disaster recovery, and industrial capacity expansion.
Concrete jacketing is broadly categorized into five main types, each with its specific materials, structural behavior, and ideal applications. These include:
- Conventional Reinforced Concrete Jacketing: Relies on increased section size and reinforcement.
- Steel Reinforced Concrete (SRC) Jacketing: Combines the compressive strength of concrete with the ductility of steel profiles.
- Fiber-Reinforced Polymer (FRP) Jacketing: Utilizes lightweight, high-tensile-strength materials with minimal intrusion.
- Shotcrete Jacketing: Offers ease of application in hard-to-access areas using sprayed concrete.
Each type serves specific needs depending on geometry constraints, loading requirements, structural damage, and environmental conditions.
1. Conventional Reinforced Concrete Jacketing
This traditional technique involves applying a new layer of reinforced concrete around the existing element. Steel bars are added for reinforcement, and the surface of the old concrete is roughened to ensure bonding. It enhances strength and stiffness and is widely used in older buildings and load-bearing upgrades.
This method typically requires the use of bonding agents, shear connectors, and closely spaced stirrups to ensure composite action. It is suitable for members with visible cracks or spalling but still possessing sufficient core strength. The enlarged section also helps reduce stress in the original member.
Best for: Residential columns, old commercial buildings, and moderate seismic upgrades.
2. Steel Reinforced Concrete (SRC) Jacketing
SRC jacketing integrates steel profiles such as angles or channels with concrete. This hybrid method boosts ductility and load capacity, making it ideal for seismic zones and structures that need significant structural reinforcement without major expansion in size.
Steel elements are first anchored to the existing member, then enclosed with reinforcement mesh before concrete is poured. The steel enhances tensile capacity, while the concrete provides compressive strength and corrosion protection.
Best for: Seismic retrofits in industrial zones, structures with high axial loads, and bridge pier strengthening.
3. Fiber-Reinforced Polymer (FRP) Jacketing
Instead of concrete, this technique uses high-strength fiber sheets (carbon, glass, or aramid) wrapped around the member. It is lightweight, corrosion-resistant, and offers a non-intrusive way to increase load-bearing capacity, commonly used in bridge piers and tight interior spaces.
Installation is typically fast, requiring only surface preparation and wrapping with epoxy-impregnated fabric. While it does not increase section size, it significantly enhances confinement, ductility, and shear resistance.
Best for: Space-restricted areas, corrosion-prone environments, and quick seismic strengthening.
4. Shotcrete Jacketing
Shotcrete jacketing uses a high-pressure hose to spray concrete onto the prepared surface. This method is efficient in areas where formwork is difficult to install, such as tunnel linings or densely populated infrastructure spaces.
A reinforcement cage is placed around the existing member, then shotcrete is applied in layers for proper build-up. Skilled application is critical to prevent rebound loss and ensure uniform thickness.
Best for: Underground structures, retrofitting in operational environments, and bridge pier jackets with access constraints.
Application of Concrete Jacketing
- Home and Residential Work
Foundation repairs, basement column upgrades, and garage post strengthening are common residential applications. Homeowners dealing with settlement issues or home additions often benefit from jacketing existing foundation elements.
- Optimizing Commercial Buildings
Changing tenants in office, manufacturing, or commercial buildings often necessitates column upgrades. Jacketing does not require progressive tenant disruption like demolition and rebuilding would.
- Modifications to Industrial Facilities
Manufacturing plants and other industrial facilities often require structural modifications to accommodate new equipment or modified processes. Jacketing has the added benefit of providing the surplus capacity necessary for installations of new massive machinery.
- Infrastructure and Public Works
Applying jacketing procedures to bridge piers, tunnel supports, or other public facilities is a widespread approach; however, public works projects often have very strict safety factors and limited building windows.
The Process of Concrete Jacketing
- Initial Assessment – Structural engineers complete all capability assessments, determine capacity requirements, and ultimately design the jacketing system. To accomplish the design, engineers do several load calculations, material selections, and construction sequencing to ensure overall project success.
- Surface Preparation Work – Existing concrete surfaces are cleaned, roughened, and prepared to achieve good bonding surfaces with the new concrete. Depending on the existing concrete surface material conditions and contamination levels, the preparation will change, including but not limited to sandblasting, mechanical scarification, or chemical cleaning.
- Reinforcement Installation – Steel rebar is placed around existing members based on engineering drawings and specifications. Uniform spacing between the rebar, lap lengths, and tie spacing will ultimately help achieve the design strength as well as achieve good composite action.
- Formwork and Bracing – Forms are constructed in a manner that contains the new concrete and maintains proper form sizes and shapes during concrete placement. The forms must be braced adequately while also maintaining leak-proof, formed joints, as concrete quality can be affected by improper forming.
- Concrete Placement and Finishing – New concrete is placed, compacted, and finished to ensure consolidation and optimal surface quality. Successful consolidation without voids is key when managing the sequence of placing and vibrating concrete to form a good bond with the existing concrete.
- Curing and Quality Control – Proper curing conditions will provide suitable curing limits for the strength development of the new concrete, while quality control tests will verify the concrete’s strength and bond quality. This phase, more than others, will determine if the jacketing system is successful and durable for the structural system.
Conclusion
Concrete jacketing offers a simple and economical alternative to rebuilding structures that require strengthening, providing repairs with minimal disruption in terms of time and cost. Concrete jacketing has become an important resource that will allow the construction industry to address structural deficiencies and enhance existing capacity. The success of the method will depend on exact engineering, skillful execution and quality construction materials.
For reliable concrete jacketing and assured quality, Brick & Bolt brings proven expertise in structural strengthening. Our team ensures your project meets all relevant safety codes and performance standards. Contact Brick & Bolt today to discuss your jacketing requirements and take the first step toward a safer, stronger structure.