One of the most searched topics in the construction space is “What concrete grade should I use?” That’s because the strength and durability of any structure depend significantly on the concrete mix ratio used.
Get it right, and your structure stands strong for decades. At Brick & Bolt, we’ve handled thousands of projects where concrete grades made all the difference. In this guide, I’ll break down everything you need to know about concrete grade tables.
Basics of Concrete Grades
Concrete isn’t just “cement + water + sand + aggregates.” Its strength varies wildly based on what ratio you are using to make it. That’s where concrete grades come in. Think of grades as a “label” that tells you how strong the concrete is after it fully hardens (usually 28 days). In technical terms, the concrete grade refers to the compressive strength of concrete in MPa or N/mm2 after 28 28-day curing period.
For instance,
For M20 Concrete Grade, M indicates mix and 20 indicates the compressive strength of concrete in MPa (megapascals) or N/mm2 after 28 days curing.
The strength of concrete is measured using a cube test. After the concrete cures for 28 days, a sample cube is tested under pressure. Based on the compression load it withstands, it is assigned a compressive strength in MPa.
- 20 MPa = M20
- 25 MPa = M25
Higher MPa means greater load capacity. The grades are crucial because not all construction works need the same strength. A garden pathway and a multi-story building require different types of concrete. That’s where concrete grades come in to make sure the mix is suitable for the intended structure.
Common Concrete Grades in Construction
- Low-grade concrete (M5 to M15)– Suitable for non-structural members and work.
- Normal high-strength concrete (M20 to M25)– Such mixes are used for unacquired strength more than M25 for residential and commercial buildings.
- High-strength concrete (M30 to M60)– Suitable for large-scale infrastructure and industrial use.
Grade | Usage |
M5 to M15 | Used for non-structural work like flooring, levelling, and pathways |
M20 | General residential construction, like RCC columns, beams, and slabs |
M25 | Commercial construction, footings, and slabs requiring strength up to 25 MPa |
M30 & above | Bridges, flyovers, and high-rise structures of heavy-duty nature |
Importance of Concrete Grades in Construction
The correct selection of the concrete grade is fundamental to a construction project’s success due to aspects such as safety, long life, and affordability.
1. Structural Safety
Using the lower grade of concrete in those parts of the building that undergo a lot of stress, such as the foundation and the beam, may cause structural cracks or the material may even collapse. The grade that is right gives the required strength to the structure to bear the existing loads, sharing its entirety and stability among the building members.
2. Cost Effectiveness
More expensive high-grade concrete is but selecting a lower grade may result in the payment of higher long-term costs because of the repairs and maintenance. You need to make sure that the upfront cost equates to the lasting durability and safety.
3. Suitability for Project Type
Each type of project, such as residential, commercial, and industrial, requires a different degree of strength for both performance and long-term endurance. That strength can be achieved by using different concrete grades.
4. Long Lifespan
The right grade ensures the proper quality of concrete for specific requirements, preventing the building from being affected by weather and load. This, in turn, is associated with the building having a longer life and requiring less maintenance.
Understanding the Concrete Grade Table
Here’s a comprehensive table that helps you compare different concrete grades based on compressive strength and mix ratio.
Grade | Compressive Strength (MPa) | Mix Ratio (Cement:Sand: Aggregate) | Uses |
M5 | 5 MPa | 1:05:10 | Non-structural work |
M7.5 | 7.5 MPa | 1:04:08 | Pathways, levelling |
M10 | 10 MPa | 1:03:06 | Flooring |
M15 | 15 MPa | 1:02:04 | Paving |
M20 | 20 MPa | 1:1.5:3 | Slabs, columns |
Above M20 | Above 20 MPa | Design Mix | Suitable for large-scale infrastructure and industrial use, such as high-rise and commercial buildings, bridges, tunnels, flyovers, etc. |
Mix Proportions for Concrete
The major factors contributing to concrete’s strength and durability are the ratio of cement, sand, and coarse gravel. The minimum consistency criteria for a mix design, as stated in IS 456:2000 and IS 10262:2019, are essential for achieving the desired durability and workability.
1. Nominal Mix (For Grades M5 to M20)
The predefined simple ratios of nominal mixes make them suitable for small-scale and low-load applications. A few examples of standard ratios are,
M15 = 1:2:4
M20 = 1:1.5:3
These budget-friendly mixes are easier to use, but they might lack accuracy for bigger or intricate projects. Factors like changes in the materials and weather conditions can have an impact on their performance.
2. Design Mix (For Grades M25 and Above)
Designs are made according to a set of requirements, which are meant to be followed very strictly in a laboratory. The mix must have the best strength-to-cement ratio, maximum resistance to weather and climate impacts, and be the most efficient for high-load and high-risk environments. In design mix, proportions vary based on material properties, project requirements, desired workability, and durability factors.
Also characterized are designs that are resistant to every challenge that they are faced with, thus, the uniformity of the high performance as well as the long and wide applications.
In short, Nominal Mixes are suitable for simple projects, whereas Design Mixes provide the strength that is needed as well as durability for complicated structures.
Key Elements Affecting Concrete Mix Proportions
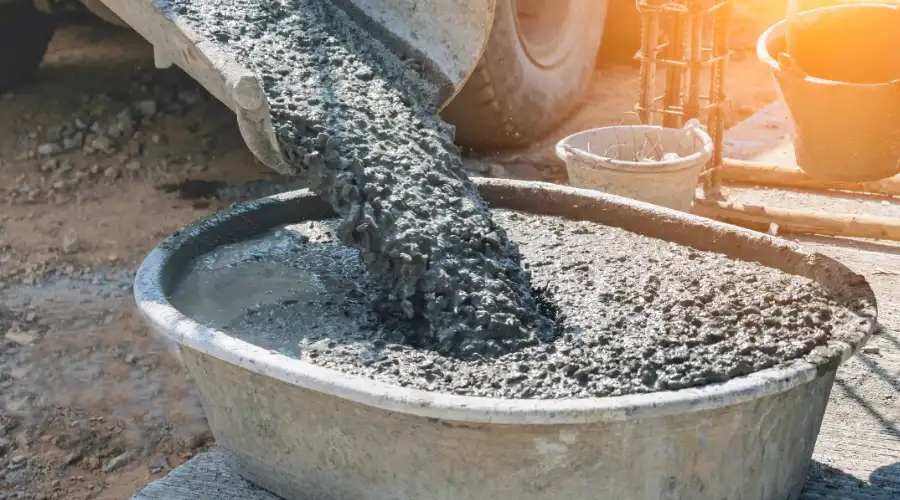
A variety of factors influence concrete mix proportions, which are necessary to ensure the strength, durability, and ability to work of the final structure.
1. Water-Cement Ratio
This ratio determines the strength of the concrete because if there is more water, the mix becomes weak and uncountable, and if there is too little water, the mix is unworkable. The most water-cement ratio that is ideal is generally in the range of 0.4 to 0.6.
2. Aggregate Quality and Size
Aggregates are materials comprising 60-80% of the concrete; they affect the strength and workability of the concrete. According to the shape of the aggregate, it increases the strength when it is angular, and it affects the workability when it is round. Depending on the aggregate size, the surface area of the aggregates and cement requirements in the mix will also change.
3. Cement Type
Each kind of cement (OPC, PPC, slag cement) has different effects on the setting time and the long-term performance of the mix. As an example, PPC has a good resistance to chemicals, while slag cement enhances durability in very severe conditions.
4. Admixtures
Plasticizers and accelerators are the kinds of chemical additives that are used in the construction industry to improve the workability, setting time, and strength according to the specific project requirements. Through an alteration in the properties of these factors, engineers get the concrete that is needed for the project to be of the required quality.
Summary
Selecting the proper concrete mix is equivalent to selecting the foundation for your vision. It’s not just a structure you’re building, you’re building safety and reliability and peace of mind over the long term.
Now that you’ve learned about concrete grades and their classifications, which determine the strength of a structure, you can make stronger decisions for your project that fit right into your work quantity and quality.
Planning your construction? Whatever the type of building, Brick & Bolt guarantees the right experts and the right concrete mix. Backed by quality assurance, lab-tested materials, and a tech-driven platform, we make building transparent and stress-free.