The adhesion of concrete is an important factor when applying new concrete to existing structures. This is especially important during slab repairs/concrete overlay installations, structural changes, or cosmetic resurfacing.
This blog delves deeper into the technology behind concrete bonding, offering a detailed look at the role and types of bonding agents, how to apply them, and the ideal conditions for their effectiveness, ultimately helping protect and strengthen our civil structures. It aims to provide practical, concrete solutions for engineers, contractors, and construction professionals.
What is Concrete Bonding?
Concrete bonding refers to the process of creating a strong adhesive connection between new concrete and an existing (old) concrete surface. Without proper bonding techniques, this connection is inherently weak due to the concrete’s brittle nature and its low tensile strength. Once hardened, concrete becomes non-adhesive, which means that simply placing new concrete over old will not ensure durability or structural continuity.
A strong bond is essential in various civil engineering applications such as structural repairs, overlays, resurfacing, and multi-layered concrete pours. In these scenarios, the integrity and load-bearing capacity of the entire system depend on how effectively the old and new layers adhere to one another.
In civil engineering practice, the bond between concrete layers can be mechanical, achieved by roughening the surface to increase interlock, or chemical, facilitated by the use of bonding agents (e.g., epoxy, latex, or polymer-based). When properly bonded, the concrete layers behave as a monolithic unit under load, distributing stresses uniformly and enhancing overall structural performance, provided the bond remains intact over time.
How to Bond Concrete?
Bonding concrete successfully involves a multi-step approach. Each phase ensures optimal adhesion and performance,
1. Surface Preparation
- Remove contaminants such as oil, paint, dust, and release agents using high-pressure washing, mechanical abrasion, sandblasting, or chemical cleaners.
- Remove any loose or deteriorated concrete laitance, or non-conforming layers.
- Roughen the surface to create texture and provide mechanical keys—recommended methods include wire brushing, grinding, or acid etching.
2. Cleaning and Saturation
- After roughening, remove debris and allow the substrate to reach a saturated surface dry (SSD) condition—moist but without surface water. This avoids drawing water out of the fresh mix and weakening bond strength.
3. Application of Bonding Agent
- Select a bonding agent suited to project demands—epoxy for heavy-duty repairs or latex‑modified mixtures for overlays.
- Apply evenly (typically with a brush, roller, or spray) to the prepared surface. Refer to the manufacturer’s instructions regarding thickness and coverage.
4. Timing and Overlapping
- Follow manufacturer guidelines: some agents require “tacky‑wet” overlap, others a tacky-dry wait before placing new concrete.
- Do not let the bonding agent cure fully unless specified. A full cure can inhibit the bond if no further treatment is applied.
5. Placement and Finishing
- Immediately place new concrete after bonding the coating. Ensure the mix design and workability align with the bonding method.
- Compact fully to eliminate voids and achieve proper interfacial contact.
6. Curing
- Cure the bonded concrete properly—moist curing for at least 5–7 days for overlays, or a minimum of 48 hours protection for epoxy-bonded repairs.
By meticulously completing these steps, you secure bond performance and structural continuity.
What is a Concrete Bonding Agent?
A concrete bonding agent is a material used to promote adhesion between new concrete or mortar and an existing concrete surface. There are two mechanisms by which these agents operate, either through chemical bonding (cross-linking between the old and new matrix) or mechanical interlocking that will fill microvoids at the interface of the substrate.
These types of material are required for bonding coats for the purpose of restoring the structural strength, on load-bearing portions, coating layers, and on floor screeds. They shall also possess minimum tensile, flexural, and compressive bond strengths at ages up to 28 days when they are tested under standard curing conditions as per ASTM C881 and IS 9103.
They minimize the risks of failure at the joints and interfaces, especially in hot spot areas such as column joints, cantilever slabs, and expansion joints.
Types of Concrete Bonding Agents
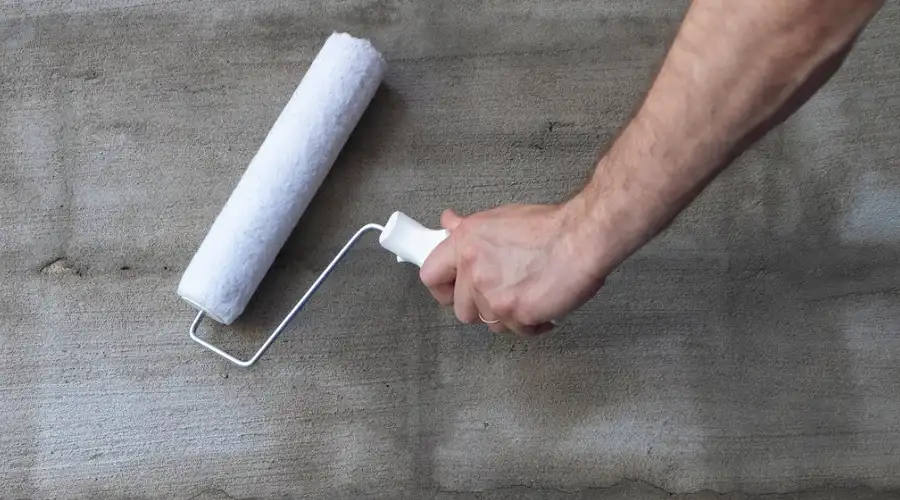
Each type comes with its own formulation benefits, limitations, and ideal usage scenarios, as described below.
1. Epoxy Resin
This two-part resin (a thermosetting epoxy) has superior adhesive strength (10~14 MPa) and chemical stability. This product is designed for structural applications such as beam-column joints, precast segment connections, and rebar anchoring. Epoxy sticks well to dry or slightly damp surfaces and has an excellent mechanical bond. However, its low permeability restricts for use as a vapor-transmitting layer, except in cases where indicated. It is also used in applications where structural strength and a long service life under heavy loads are required.
2. Acrylic Latex
Acrylic latex is a one-component water based polymer used to increase the workability and the durability of cement-based mixes. It is superior in tensile strength, shrinkage control, and adhesion to a surface. It is suitable for floor toppings and patch repairs and has excellent alkali and UV resistance for use as exposed concrete works. More specifically, it is more useful in enhancing cohesion and workability of cement mortars for large floor area applications.
3. Latex Emulsions
Latex emulsions are polymeric additives that improve the workability and impermeability of repair mortars. The best ones to use for vertical or overhead repairs, where you need tack retention and the right amount of slump resistance. The fine molecular structure also makes for a predictable bond, even on irregular or intricate shapes, typical in structural reinforcement & restoration.
4. Styrene Butadiene Latex (SBR)
SBR is a synthetic rubber latex additive to improve on adhesion, flexibility, and waterproofing. It is a popular adhesive for wet areas and waterproofing applications, including bonding of cementitious slurries. Because SBR is chloride-resistant and has enhanced freeze-thaw resistance, it is commonly used in marine or underwater structures. It forms a durable seal in the presence of water and chemicals.
5. Polyvinyl Acetate Latex (PVA)
PVA (polyvinyl acetate) is an inexpensive, easy-to-use glue that works in dry, indoor conditions. It creates a suitable bond for non-load-bearing repairs and is easy to use. But the water-solubility of the pastel ink restrains its usage in wet and outdoor places. For drywall repairs, internal crack filling, and surface levelling under low load stresses, PVA is your best bet.
Importance of Concrete Bonding Agent
Bonding agents offer multifaceted benefits in concrete construction,
- Enhanced Adhesion: Boosts bond strength beyond mechanical friction and cement hydration alone.
- Structural Integrity: Minimizes delamination and layer separation, especially under differential loading.
- Flexibility Control: Polymers reduce brittleness and shrinkage in overlays, reducing cracking.
- Water and Moisture Resistance: Many agents improve permeability characteristics, prolonging life in wet conditions.
- Chemical Resilience: Epoxies, in particular, provide resistance to solvents, chemicals, and environmental degradation.
- Efficient Repairs: Agents permit thinner, stronger overlays, offering time and material savings.
Bonding agents are not optional—they are vital wherever performance demands exceed simple overlay or patch adhesives.
Features of Concrete Bonding Agent
Key properties define effective bonding agents,
Feature | Description |
Compatibility | The bonding agent must align with the chemical composition, pH, and moisture properties of the concrete. |
Formulation | Available as liquid coatings or admixtures, some may be cement-modified to support early hydration. |
Solids Content | High solids content (45-55%) ensures strong film formation. Lower solids content may lead to weaker bonds. |
Workability | Epoxies often require precise mixing and temperature control, while latex-based agents are simpler and easier to handle. |
Cure Dynamics | Tack time and cure time determine the optimal window for applying overlay materials. |
Environmental Performance | Waterborne and low-VOC bonding agents are gaining preference due to their environmentally friendly nature. |
Choosing the Right Concrete Bonding Agent
Choosing the right glue or adhesive for your project can be a daunting task, especially with so many options available for different materials and applications.
- Epoxy mortar resins are often chosen for structural repairs based on their compressive strength, chemical resistance, and relatively low cost.
- While acryl-latex or PVA emulsion-based latex agents are often used for non-structural overlayments, re-surfacing or ones in which decorative toppings are to be installed.
- Styrene-butadiene rubber (SBR) is an ideal solution for areas with moist conditions, such as basements, tanks, and rooftops, as it provides great waterproofing and flexibility.
How to Use Concrete Bonding Agent?
While the application may seem simple, attention must be paid to each step and product requirements. So let’s break down the process,
Substrate Preparation
The foundation of effective bonding lies in proper surface preparation. The concrete surface should be thoroughly cleaned to remove dirt, oils, curing compounds, or paint residues. This can be done via pressure washing, sandblasting, or mechanical grinding. More importantly, the surface must be roughened to create a mechanical profile, enhancing adhesion at the microscopic level.
Once the surface is cleaned and textured, ensure it is brought to a Saturated Surface Dry (SSD) condition. This means the concrete is moist but not visibly wet. Applying bonding agents on either a bone-dry or overly saturated surface can reduce their effectiveness.
Mixing and Application
Certain latex-based agents may require dilution (e.g., 1:1 with clean water) or blending with a cement slurry, depending on the manufacturer’s instructions. For example, re-emulsifiable PVA or acrylic latex can be applied as a stand-alone bonding coat or combined with cement to improve interface grip.
Use appropriate tools such as a brush, roller, or spray gun to apply the bonding agent evenly across the entire surface. Avoid overapplication, as pooling may cause weak spots or longer tack times.
Timing is key in this phase. Some agents require the fresh concrete to be applied while the bonding layer is still tacky, while others may need it to dry slightly until it forms a sticky film. If the agent dries completely and is not reactivated by the overlay mix, the bond may fail. Always refer to the product’s datasheet for tack time recommendations.
Concrete Placement and Finishing
Once the bonding coat is ready, place the new concrete mix promptly. It’s important to compact it properly to eliminate air gaps that could weaken the interface. Avoid any mechanical disturbance until the initial set is achieved. Use trowels or vibrators gently so as not to displace the bonding layer.
Curing and Bond Testing
Proper curing is just as important as application. For cementitious overlays, maintain moisture by covering the surface with wet burlap, curing blankets, or misting for at least 5 to 7 days. Epoxy-based agents often set faster but still require a minimum of 48 hours before exposure to load or stress.
To verify the success of the bond, perform field testing such as pull-off tests, hammer tap evaluations, or even core sampling for large-scale structural projects. These confirm that the bond has achieved its required tensile and shear strengths.
Conclusion
Concrete adhesion is a highly accurate technique, and it is about maintaining continuity and serviceability throughout structures. Attaining a successful bond is achieved by specific surface preparation, highly engineered adhesives, accurate timing, and supportive curing.
When properly constructed, the juncture between old and new concrete performs as a monolithic structure able to withstand physical, environmental, and chemical attack. In the construction and renovation industry, bonding agents are a necessity for extending longevity and adding life to both high and low-performance projects.