Cement is one of the most important binding materials used in construction. Among the many types available, Ordinary Portland Cement (OPC) is a widely used and versatile option. It can be mixed with other materials to achieve the right cement ratio for different construction needs. From building homes to constructing skyscrapers, OPC plays a key role.
Read this blog to learn more about OPC and its uses.
What Is OPC in Construction?
Ordinary Portland Cement (OPC) is the general type of cement renowned for its versatility and high early strength; OPC serves as the primary binding material in concrete, mortar, and plaster for a variety of structures, including buildings, bridges, and roads. It is classified into three main grades based on their compressive strength: OPC-33, 43, and 53. Ordinary Portland cements are hydraulic in nature, which means they set and harden when mixed with water, making them a crucial component for durable and robust construction.
Composition & Manufacturing Process of OPC
Composition of Ordinary Portland Cement
OPC is mainly composed of limestone, clay or shale, Gypsum and other minor constituents, including magnesia, sulphur trioxide, and alkalis.
Their composition percentage is as follows:
Calcium Oxide | 60-67% |
Silicon Dioxide | 17-25% |
Aluminum Oxide | 3-8% |
Ferric Oxide | 0.5-6% |
Magnesium Oxide | 0.1-4% |
Sulfur Trioxide | 1-3% |
Step-wise Manufacturing Process
- Crushing and Grinding: Raw materials like limestone and clay are quarried, crushed, and ground into a fine powder.
- Proportioning and Blending: The raw materials are mixed in precise proportions to achieve the desired chemical composition.
- Preheating: The blended raw mix is preheated in a preheater tower to start the chemical reactions.
- Calcination in Kiln: The preheated mix is fed into a rotary kiln and heated to about 1450°C. Here, chemical reactions form clinker—hard, nodular material composed mainly of calcium silicates and aluminates.
- Clinker Cooling: The hot clinker is rapidly cooled to preserve its reactive properties.
- Grinding: Clinker is mixed with 3–4% gypsum and ground into a fine powder to produce OPC. Gypsum works as a retarder in cement, and it controls the rate at which OPC sets after mixing with water. Without gypsum, the rapid reaction of tricalcium aluminate (C3A) with water would cause “flash setting,” making the cement harden almost immediately and rendering it unworkable.
- Packaging and Storage: The finished cement is stored in silos and packed for distribution.
Grades of OPC & Their Uses
OPCs are categorized into different grades based on their compressive strength, indicated in megapascals. These grades indicate the strength and quality of the cement.
Here are some of the primary types of OPC,
OPC 33 Grade
The compressive strength is 33 MPa after curing for 28 days for OPC 33 Grade. It is generally used for common construction that does not need high strength. Their main applications are small residential buildings, flooring, and plastering.
OPC 43 Grade
The compressive strength is 43 MPa after curing for 28 days for OPC 43 Grade. They are used in reinforced concrete structures like columns, beams, slabs, and bridges. They provide a good balance between strength and workability.
OPC 53 Grade
OPC 53 Grade has a compressive strength of 53 MPa after 28 days of curing. It’s a high-strength cement. It is ideal for high-rise buildings, industries, and infrastructure projects like bridges and highways. They provide fast setting and hardening. This makes it suitable for construction work.
Properties of Ordinary Portland Cement (OPC)
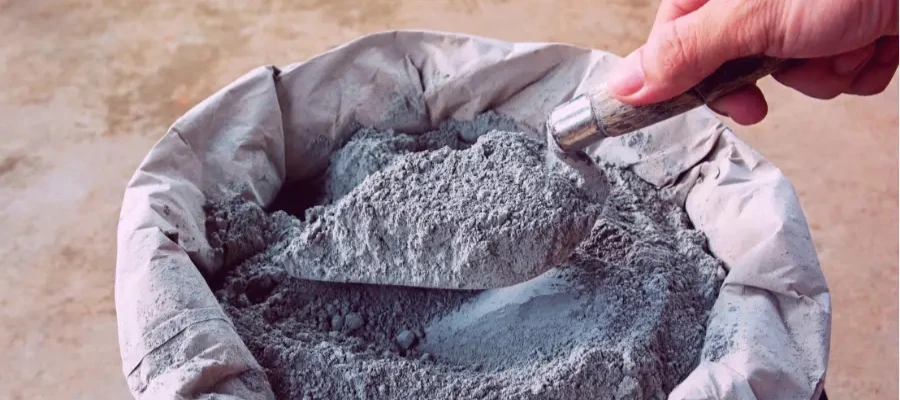
Physical Properties of Ordinary Portland Cement
Fineness
Fineness refers to how small the cement particles are. The smaller the particles, the larger the surface area they provide for the chemical reaction with water (called hydration). This leads to faster strength gain and improved workability of the cement paste.
For Ordinary Portland Cement (OPC):
- The fineness is usually not less than 225 m²/kg, measured using Blaine’s air permeability apparatus.
- About 95% of OPC particles are smaller than 45 microns, and the average particle size is around 15 microns.
Finer cement helps in better bonding and quicker setting, which is important for strength development in construction.
Setting Time
The time taken by cement to transform from a plastic state to a hardened state when mixed with water is called the setting time. OPC has an initial setting time of at least 30 minutes and a final setting time not exceeding 600 minutes. This offers sufficient time to mix, transport, and place the concrete before it hardens.
Soundness
Soundness refers to the cement’s ability to resist unwanted expansion after it has set. If the cement expands too much after setting, it can cause cracks, disintegration, or deformation in the hardened structure. The Le Chatelier method is commonly used, with expansion not exceeding 10 mm, and the autoclave test should show less than 0.8% expansion. High soundness ensures the long-term durability of structures.
Compressive Strength
The compressive strength of cement is the load-bearing capacity after curing. OPC is primarily characterized by its compressive strength, which determines its performance in structural applications. It is commonly classified into grades such as 33, 43, and 53, based on the strength achieved after 28 days of curing. For example, 53 grade cement signifies that a standard cement cube will attain a compressive strength of 53 N/mm² (MPa) or 530 kg/cm² after 28 days, under controlled conditions.
Heat of Hydration
The heat of hydration is the amount of heat released when cement reacts with water during the setting and hardening process. The heat generated is mainly due to the hydration of tricalcium aluminate (C3A) and tricalcium silicate (C3S), two principal compounds in OPC. OPC releases approximately 230 J/g after the initial 60 minutes. Comparatively, low-heat cement (a specialised variant) restricts heat to ≤272 kJ/kg at 7 days.
Normal Consistency
Standard consistency (also called normal consistency) refers to the ease with which a cement paste (a mix of cement and water) can flow under standard conditions. For dry mortar (cement and sand) or dry concrete (cement, sand, and aggregates) to reach a workable state, the right amount of water is essential. Therefore, maintaining an optimal water-cement ratio is crucial to achieve the desired workability of the mix.
Chemical Properties of Ordinary Portland Cement
When the chemical compositions of Ordinary Portland Cement are combined with water, these constituents react chemically, forming the following compounds, offering respective properties to the cement:
- Tricalcium Silicate (C3S)- hydrates quickly, offering high early strength
- Dicalcium Silicate (C2S)- hydrates more slowly, giving later strength.
- Tricalcium Aluminate (C3A)- reacts rapidly with water and is responsible for the initial set and early heat generation, but excessive C₃A can make cement vulnerable to sulfate attack.
- Tetracalcium Aluminoferrite (C4AF)- helps in the maintenance of colour. It has a minor effect on strength.
Advantages of OPC in Construction
- Versatility: OPC is a well-known, versatile option that can be used in various construction applications. It can be used for different construction needs, such as buildings, bridges, dams, roads, and other projects.
- Strength and Durability: OPC possesses excellent compressive strength, allowing structures to bear heavy loads. It has great resistance to weathering, presenting longevity and stability to structures.
- Easily Available and Affordable: You can purchase this cement across India cost-effectively as it involves mass production.
- Compatibility with Other Materials: You can use OPC with the combination of other materials like aggregates, water, and additives, allowing builders to customise their properties. This compatibility promotes producing different types of concrete and mortar mixes customised to specific project requirements.
Limitations of OPC in Construction
- High Carbon Footprint: OPC’s manufacturing process emits a considerable amount of carbon dioxide (CO2) into the environment. It can play a significant role in environmental pollution.
- Energy Intensive: The production of OPC requires high temperatures, demanding notable energy consumption. This energy intensity results in the consumption of fossil fuels and further contributes to greenhouse gas emissions.
- Cracks and Shrinkage: OPC can be vulnerable to shrinkage and cracking as it cures, impacting the structural integrity of the building. To avoid this, you need to take extra care, such as using reinforcements or expansion joints, to mitigate the issue.
- Slow Setting Time: When compared to other types of cement, such as quick-setting cement, OPC has a slow setting time. This slower setting rate can increase construction time, causing delays in the completion of projects.
- Limited Resistance to Chemical Attacks: Ordinary Portland Cement (OPC) does not strongly resist some chemical attacks. For example, it can get damaged when exposed to sulfates or harsh chemicals. In such situations, it is better to use other types of cement or take extra steps to protect the structure.
OPC vs. Other Types of Cement (PPC, PSC)
Feature | OPC (Ordinary Portland Cement) | PPC (Portland Pozzolana Cement) | PSC (Portland Slag Cement) |
Composition | OPC is made mainly from clinker (60–67% calcium oxide, 17–25% silicon dioxide) and 2–5% gypsum. | PPC is produced by blending OPC clinker with 15–35% pozzolanic materials such as fly ash. | PSC is manufactured by mixing OPC clinker with up to 50% granulated blast furnace slag. |
7-Day Strength | OPC typically achieves a compressive strength of 15.5–18 MPa after 7 days of curing. | PPC usually reaches a compressive strength of 13.5–14.6 MPa in 7 days. | PSC generally attains a compressive strength of 13.7–15.3 MPa after 7 days. |
28-Day Strength | OPC can reach 33–53 MPa compressive strength after 28 days of curing. | PPC reaches a 33 MPa (minimum standard) up to around 45 MPa compressive strength at 28 days, as per BIS requirements. | PSC also attains a 40 MPa (minimum standard) up to around 45 MPa compressive strength after 28 days of curing. |
Early Strength Gain | OPC gains strength rapidly, reaching about 70% of its 28-day strength in the first 7 days. | PPC gains strength more slowly, reaching about 60% of its 28-day strength in 7 days. | PSC also gains strength slowly, similar to PPC, with steady strength development. |
Setting Time | OPC has an initial setting time of at least 30 minutes and a final setting time within 600 minutes. | PPC has a slightly longer setting time than OPC, providing more workability for mixing. | PSC has a setting time similar to PPC, which is generally longer than OPC. |
Heat of Hydration | OPC produces a high heat of hydration, which can increase the risk of thermal cracks in mass concrete. | PPC produces less heat of hydration than OPC, reducing the risk of thermal cracking. | PSC has the lowest heat of hydration, making it ideal for mass concrete and hot climates. |
Durability | OPC is less durable in aggressive environments and is moderately resistant to chemicals. | PPC is more durable and offers better resistance to sulphates and chlorides. | PSC is the most durable, providing excellent resistance to chemicals and marine exposure. |
Environmental Impact | OPC has a higher carbon footprint because it uses more clinker and produces more CO₂ emissions. | PPC has a lower carbon footprint due to the use of industrial by-products like fly ash. | PSC has the lowest carbon footprint, as it contains a high proportion of slag. |
Cost | OPC is generally more expensive than PPC and PSC. | PPC is usually 5–10% less expensive than OPC, depending on local availability. | PSC is often the most cost-effective, especially where slag is readily available. |
Best Use Cases | OPC is best used when high early strength and fast construction are required, such as in precast elements or high-rise buildings. | PPC is ideal for mass concrete works, plastering, and structures needing long-term durability. | PSC is recommended for marine structures, sewage treatment plants, and foundations exposed to chemicals. |
Availability | OPC is widely available in most regions and is the most commonly used cement type. | PPC is also widely available and commonly used in many construction projects. | PSC is available in most regions, though availability may depend on local slag supplies. |
Common Applications of OPC in Construction
- Ordinary Portland Cement (OPC) presents high strength and reliability; thus, this cement is commonly used in residential buildings, including foundations, walls, and slabs.
- OPC is useful for building pavements and roads, offering durability and load-bearing capacity.
- OPC is also used in precast concrete products such as blocks, pipes, and tiles, and forms the core material for structural elements like beams, columns, and slabs, ensuring stability and longevity in diverse construction projects
Tips for Storing OPC Properly
- To maintain the quality of cement, store OPC cement in dry, weatherproof areas to prevent moisture exposure, which can cause the cement to harden and become unusable.
- Moisture can cause the cement to harden prematurely, making it useless. Use sealed containers or bags and keep them off the ground to avoid contact with damp surfaces. Regularly check storage conditions to ensure the cement remains dry and in good condition.
In conclusion, Ordinary Portland Cement (OPC) is a vital material in modern construction, known for its high early strength, versatility, and reliability. From small residential homes to large-scale infrastructure projects, OPC plays a major role in ensuring strong and durable structures. Understanding its properties, grades, advantages, and limitations helps in choosing the right type of cement for different construction needs. However, selecting the right materials is just one part of quality construction. To ensure expert guidance, proper execution, and trusted materials, choose a reliable partner like Brick & Bolt, India’s most trusted tech-enabled construction company for end-to-end building solutions.
FAQs
OPCs are categorized based on compressive strength into different grade types.
Dicalcium silicate helps in later strength development.
Soundness ensures that cement does not expand excessively after setting. This is for preventing cracks.
OPC generally has a shelf life of about three months if stored properly in a dry place. It is best to use it within this time to ensure it is effective.
Yes, OPC can be used for underwater projects, but it is better to use special cement designed for underwater conditions.
OPC starts gaining strength quickly, reaching about 70% of its strength in the first 7 days. It achieves full strength after 28 days.
OPC manufacture requires a large amount of energy, and CO2 emission occurs in the process. Measures are currently being taken to alleviate these effects and to look for less damaging solutions.