Sandblasting is a high-pressure surface preparation technique used in construction to clean and smooth materials like steel, concrete, and masonry. It involves propelling abrasive materials such as silica sand or steel grit against surfaces to remove rust, old paint, grime, or imperfections. This process is essential before applying coatings, waterproofing, or paint, ensuring better adhesion and durability. Commonly used in bridge repairs, structural steel preparation, and façade restoration, sandblasting delivers a clean, uniform finish. It saves time, enhances surface quality, and improves the longevity of construction materials by ensuring they’re free of contaminants before finishing work begins.
What is Sand Blasting?
Sandblasting is a method that involves the use of compressed air or water to accelerate abrasive particles at very high velocities toward a surface. The prime motive behind this treatment is to alter the surface in some way, such as cleaning, smoothing rough surfaces, or creating a specific texture. Originally, the abrasive used was silica sand, which gave the process its name, sandblasting. However, the risks associated with inhaling silica dust (silicosis) have made the industry move toward safer alternatives such as aluminium oxide, steel grit, and glass beads.
Types of Sandblasting
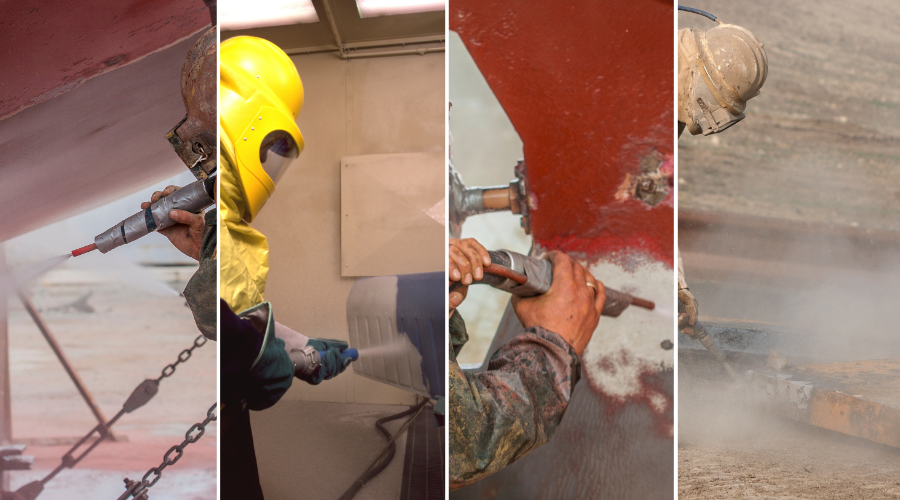
Dry Sandblasting
Dry sandblasting utilises a force of compressed air to propel abrasive grains at high speed against a surface. Heavy rust, paint, or scale removal is for its great appeal. It may also prevent glare if properly vented, while keeping the operator protected by using the necessary dust masks.
Wet Sandblasting
Here, in wet sandblasting, water is combined with abrasive substances before it is blasted onto the surface. This helps to reduce dust and heat buildup caused by abrasion, thus providing a clean environment for abrasive treatment of sensitive surfaces or inside a work area. It almost guarantees low chances of deformation, even if thin metal is in use.
Vacuum Sandblasting (Suction Blasting)
In vacuum sandblasting, the abrasive material is blown onto a surface and collected immediately by a vacuum system. The presence of this vacuum system matters insofar as controlling the mess caused by abrasive media makes it the best choice for applications in sensitive environments indoors or near other forms of machinery.
Pressure Blasting
The second blasting, an aggressive one, is the pressure blasting that uses streams of either compressed air or water to forcefully push abrasive media through a narrow nozzle. It is highly suited for surface cleaning and preparation when dealing with thick coatings, corrosion, or industrial cleaning.
Application of Sand Blasting
1. Preparing Concrete for Coating or Bonding
Sandblasting is widely used to prepare concrete flooring for bonding or coating. By removing contaminants, old paint, and surface irregularities, sandblasting creates a roughened surface that enhances the adhesion of new coatings, sealants, and overlays. This process ensures long-lasting and durable finishes.
2. Cleaning Structural Surfaces
In construction, sandblasting is applied to clean steel, metal, and structural surfaces, such as beams, pipes, and frameworks. It removes rust, dirt, old paint, and corrosion, providing a clean surface that allows for better adhesion of protective coatings, improving the structure’s durability.
3. Restoring Historical Structures
Sandblasting is essential in the restoration of historical buildings, where it is used to gently remove layers of grime, paint, and surface deterioration without damaging the underlying stone, brick masonry. This helps in preserving the integrity of the original material while preparing it for refinishing or protective coatings.
4. Surface Preparation for Waterproofing
Sandblasting helps prepare surfaces, like foundations and basements, for waterproofing treatments. It ensures that waterproofing materials bond effectively to the surface, providing reliable moisture protection.
5. Concrete Floor Coating Removal
Sandblasting is used to remove epoxy, urethane, and other floor coatings in industrial settings, exposing the bare concrete for recoating. This is especially useful in factories or warehouses where surface preparation is crucial for new coatings.
In construction, sandblasting is vital for surface preparation, cleaning, and ensuring the longevity of materials used in various projects.
Advantages and Disadvantages of Sand Blasting
Advantages
- Compatible with Multiple Materials: Works effectively on steel, concrete, brick, stone, and softer composites.
- Improved Coating Adhesion: Creates a non-directional, roughened surface that allows better bonding of paints, sealants, and waterproofing layers.
- Versatile Outcomes: Can be adjusted for heavy-duty cleaning or fine surface texturing depending on project needs.
- Ideal for New Builds & Renovation: Suitable for both fresh constructions and restoring aged surfaces.
- Chemical-Free Cleaning: Removes contaminants, rust, and old coatings without using corrosive chemicals.
- Enhances Durability: Prepares substrates in a way that prolongs the life of applied protective systems.
Disadvantages
- Blast Only the Section: Without masking off the surroundings, target area blasting can be challenging.
- Wearing Down of the Machine: The abrasive nature of the process causes wear of nozzles and internal parts.
- Sludge Generation: Especially in wet blasting, sludge needs to be managed and disposed of properly.
What Are the Materials Needed for Sand Blasting?
Different materials and equipment are essential for a successful sandblasting operation,
Abrasive Materials
- Aluminium Oxide: Hard, reusable, and aggressive. Ideal for surface profiling and cleaning ferrous metals. Offers consistent performance and is cost-effective in repetitive blasting.
- Steel Grit/Shot: Heavy-duty abrasives used in large-scale industrial and structural cleaning. Steel grit is angular for etching, while shot is round for peening and polishing.
- Glass Beads: Silica-free, spherical media that produce a smooth, satin finish on non-ferrous metals. Ideal for cosmetic finishing.
- Plastic Media: Designed for delicate surfaces like composites and aluminium. Commonly used in aerospace for paint stripping without base material damage.
- Baking Soda: Water-soluble and soft. Effective for fire damage restoration, grease removal, and sensitive substrates like chrome or aluminium.
- Silicon Carbide: Extremely hard and fast-cutting. Suitable for etching glass, stone, and hard metals where deep penetration is needed.
- Corn Cob & Walnut Shells: Biodegradable, low-impact abrasives for wood, brick, and historic preservation work.
Equipment
- Blasting Pot: This equipment holds and releases the abrasive.
- Compressor: Supplies the high-pressure air or water necessary.
- Nozzle: Imparts direction to abrasive materials towards a surface.
- Protective Equipment: Helmets, gloves, suits, and respirators are all important for safety.
Sand Blasting Process
Surface Inspection
The surface to be treated must first be inspected. It will ascertain the degree of contamination, rust, paint, and other imperfections that need removal. This inspection also sets the direction for the choice of blasting materials and methods.
Select the Right Abrasive
An abrasive is selected as per the surface upon which it is to be employed and the surface characteristics required. Steel grit may be selected for heavy rust removal, while glass beads or baking soda may be needed for delicate surfaces.
Assemble the Equipment
The blasting pot is filled with the selected abrasive, and the compressor is hooked up for air or water pressure. The nozzle and hoses are secured when everything is set, allowing for steady abrasion in the direction of work.
Wear Protective Clothing
Safety is a paramount concern in sandblasting. Sandblasters must wear protective clothing, gloves, a respirator or helmet, and goggles. This is to guard from flying debris, dust, or abrasive particles.
Blasting Operation Begins
The operator should start blasting the surface with an abrasive jet at a correct distance and angle of abrasives. The abrasive impacts the surface to overcome contamination or to alter the texture as required.
Monitoring and Adjustment
During the blasting operation, the operator monitors the changes in pressure, movement of the nozzle, and the effectiveness of blasting. Causes of adjustment may include changes in the speed of the nozzle, its angle, or pressure to achieve the best outcome.
Cleaning Up the Area
After blasting, clean up the surface and the surrounding area to eliminate any residual abrasive material and dust. With vacuum or wet blasting, this step is quicker and less messy.
Surface Inspection and Post-Treatment
Ranked last in inspection for uniformity and completeness, the treated surface is ready for painting, coating, or even further processing if intended.
Conclusion
Sandblasting is a powerful and versatile technique used across many industries for cleaning, finishing, and restoring surfaces. It will clean rust from machines as well as prepare metals for painting, or it will impart a decorative texture to a material, giving consistent results. Greater development of the equipment and safer media imply that surface treatment aerosolisation continues to be a treatment of choice for technicians balancing time, precision, and safety.