Pumpable concrete is a multifunctional and highly effective material for contemporary construction, enabling uninterrupted operations and increased productivity on the construction site. Unlike conventional concrete, pumpable concrete is designed to be easily and continuously pumped through concrete pump, indicating its suitability for sites that are hard to access and in challenging conditions.
In this post, we will discuss pumpable concrete, including its importance, benefits, and key considerations for using it in construction.
An Overview of Pumpable Concrete
Pumpable concrete is a specially designed concrete mixture that can flow smoothly through pipelines or hoses when pumped. Unlike standard concrete, it must have specific characteristics, including uniform consistency and optimal proportions of aggregates, cement, and water.
These properties ensure the concrete can travel without causing blockages in the pump system. Pumpable concrete is a suitable option for such challenging undertakings as multi-storey buildings, where traditional concrete delivery systems would cause the work to be slow and even impractical, offering improved worksite productivity and reduced labour costs.
Types of Pumps Used for Pumpable Concrete
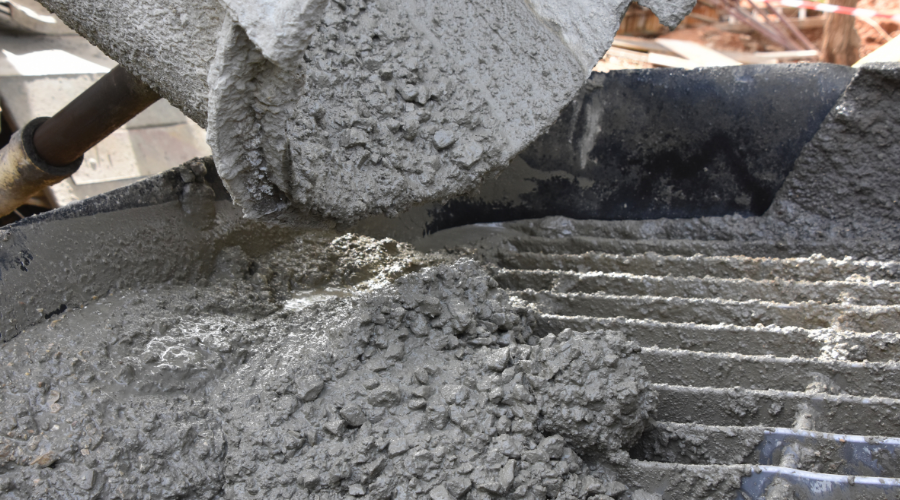
So the various systems to use for pumping concrete are,
1. Boom Pumps
Boom pumps enable the pumping of concrete over long distances; they are transportable and feature a high boom that can extend and rotate. They offer vertical and horizontal placement of the concrete and are hence suitable for high-rise buildings or large constructions.
2. Line Pumps (Trailer Pumps)
Line pumps convey concrete over shorter distances through a series of hoses and are thus less expensive than boom pumps. Line pumps come on a trailer, which allows them to be moved to the place where the construction of the house or slab is taking place. These are generally the best equipment for simple to medium construction tasks in towns and cities.
3. Other Types (Less Common)
Some of the less common types of pumps are tower cranes having pump facilities and grout pumps. Tower cranes can also pump while placing concrete, while grout pumps are used to inject cementitious grout that is used to fill voids or cracks in concrete.
Benefits of Pumpable Concrete
Pumpable concrete can do several things in construction projects,
- Passes easily through pipes or hoses, which can even access difficult-to-reach areas.
- This reduces labour and material handling expenses, which reduces the time required.
- Greater control and precision of the placement of concrete result in a more secure structure.
- The traditional method of manual transportation and pouring is replaced with a mechanical one, making the project faster.
- Such mixtures are not designed to clog pipes but to ensure a good and uninterrupted flow without interruption for a longer life cycle of the materials used and to prevent incidents in the construction site.
- The practice of manual handling is reduced to a minimum, which leads to fewer injuries to workers.
Important Aspects of Pumpable Concrete
Pumpable concrete comes with a list of requirements that are necessary to be fulfilled to allow for a smooth flow of the material through the pipelines without interference or stoppage by the material.
- The flowability of the mix is the most important aspect, which keeps the consistency of the slurry in such a way that it is unsegregated and can be easily pumped into the pipeline with as little friction as possible.
- Also, cohesion is vital in that the absence of it would automatically lead to the mixture being ruined; thus, when pumped the material must remain the same.
- Standard granulometry is the key to ensuring that the aggregate particles do not obstruct the pump while they are being conveyed.
- Further, the stability and resistance should remain the same; the concrete, after it sets, should never be seen in a deteriorated state.
Requirements of Pumpable Concrete
1. Ease of Handling
Pumpable concrete should have high workability so that it can easily travel through the pump and into the pipeline without segregation or clogging the system. This is done by using a good mix, usually composed of fine aggregates, a controlled water-cement ratio, and chemical admixtures like concrete plasticizers and superplasticizers that improve flow.
2. Consistency
It is very important for pumpable concrete to be consistent, meaning that the mixer is of the same quality throughout, making it easier to pour and flood without causing any resistance. Pumping concrete with a slump of 50 to 100 millimeters is usually the most recommended as it will be able to strike a balance between flowability and cohesion.
3. Size and Grading of Aggregates
The size of the aggregate and its grading have a significant effect on the pumpability of the concrete. Well-graded aggregates minimize the friction force in the pipeline and thus avoid blockages. In pumpable concrete, the particle size of the aggregate is normally kept under 40 mm to allow the material to flow unobstructed.
4. Controlled Water-Cement Ratio
Pumpable concrete is supposed not to change, seeking to prevent the segregation that takes place when the heavier components (such as coarse aggregates) slip the finer grains (cement and sand) through. To achieve a stable mix, the water-cement ratio is optimally adjusted, and suitable admixtures are also used.
5. Admixtures
Chemical admixtures, such as concrete retarders, plasticizers, superplasticizers, and air-entraining agents, are the most common additives to improve the pumpability of concrete. These admixtures not only help maintain the proper consistency and workability of the mixture but also prevent the sudden start of the hydration process..
6. Cement and Fine Content
The type and amount of cement and fine particles, such as sand or pozzolanic materials, used in the combination are crucial to achieve the cohesiveness of the concrete. A higher percentage of fine particles in the mix makes the concrete more flowable, thereby reducing the risk of segregation.
Factors Affecting the Performance of Pumpable Concrete
- Concrete Proportioning
For the easy flow of concrete through pipes, the correct balance between cement, aggregates, and water is of the utmost importance. The right proportion not only minimizes clogging but also ensures an efficient pumping process.
- Water-Cement Ratio
A high water-cement ratio could result in segregation; hence, the mix will be difficult to handle and pump. A low ratio of water to cement will result in a very thick mixture, which will also be hard to pump. The ultrahigh performance can boast only of the right w/c ratio, which will allow workability and pumpability.
- Aggregate Size
The smaller the aggregates, the less resistance there will be in the pumping process, which will lead to better and smoother flow. Higher grain sizes can impede the transfer of material and require more energy for pumping.
- Slump
The mix’s workability is determined by the slump. A high slump indicates that pumping is done the right way, while a slump that is too high can lead to instability and separation. The main point of achieving good pumping effectiveness is to have an ideal slump.
- Pumping Pressure
To cover long horizontal distances or great vertical heights, a high degree of pressure is demanded, yet too much pressure may lead to segregation and blockages. The main thing in this regard is to find the right mix characteristics that can balance the pressure.
- Admixtures
Using plasticizers and superplasticizers to enhance the workability of the mix can simplify pumping and induce the flow without the necessity of adding water. Therefore, the plasticizer is also one way of realizing pumpability when it reduces the moisture content.
- Temperature
At high temperatures, the concrete setting is accelerated, and the mix is harder to pump. Use of cool air and delaying agents will make it work well, most probably in very hot weather and stabilize the consistency.
Consideration of Mix Design for Pumpable Concrete
The factors are as follows,
1. Aggregate Selection and Gradation
The inclusion of both large and small fractions of aggregates in the correct proportions is the key to a good pumpable mix, which means a mix of aggregates should be well-graded. For smooth pumping performance, the maximum size of crushed (angular) aggregates should not exceed one-third of the internal diameter of the hose or pipeline, considering the geometric constraints of their cubical shape. In the case of rounded or uncrushed aggregates, their size can be slightly larger—limited to 40% of the pipe’s internal diameter—due to their better flow characteristics.
2. Cementitious Materials Content
A minor increase in cement quantity can lead the mix to flow quickly, and such an action indirectly assists in minimizing the force of resistance during the piping stage.
3. Water-Cement Ratio and Slump
An appropriate water-cement ratio that enables the material to have pumpability is of the utmost importance. The slump value should be in the range of 50–100 mm, allowing the mixture to flow sufficiently to prevent segregation.
4. Admixtures
The improved workability of pumpable concrete is largely achieved through the use of chemical admixtures, such as plasticizers or superplasticizers. These admixtures are crucial in enhancing flow without increasing water content.
Conclusion
The pumpable concrete is a necessity for modern construction that can effectively and accurately be delivered to the most difficult or elevated locations. Largely, its efficiency depends on a well-designed mixture, wherein the choice of the right aggregate, a well-balanced water-cement ratio, and the application of admixtures for the improvement of workability and segregation prevention are principal factors.
In a word, pumpable concrete provides construction teams with an opportunity to achieve better labor productivity, lower costs, and greater project success, thus it is the customer’s newest best bet in the construction industry.