Glass concrete is reshaping modern construction by blending strength, sustainability, and visual appeal through the use of recycled glass and glass fibers. For architects, it opens creative possibilities, from facades to feature elements, without compromising on performance. Engineers and builders value its lightweight nature, which enhances structural efficiency while maintaining durability.
As sustainability takes center stage, glass concrete offers a forward-thinking solution that reduces waste and boosts resource efficiency. For manufacturers and suppliers, it presents a unique opportunity to contribute to the green building movement with a smart, future-ready material that aligns with evolving construction needs.
What is Glass Concrete?
Glass concrete is a composite material consisting of encapsulated fractions of recycled glass particles that are either partially or completely replacing a standard aggregate, gravel or crushed stone matrix. It combines cement, water, and crushed glass particles to produce glass as a construction material that is not only structurally sound but also aesthetically pleasing and eco-friendly. Glass concrete can be designed for structural applications, in some cases, to meet load-bearing requirements and in others, as decorative applications in contemporary buildings.
Composition and Process of Using Recycled Glass in Concrete
Material Selection:
Recycled glass, which can come from either post-consumer or industrial sources, is processed. This involves washing to remove contaminants, sorting by colors and types, and then crushing down to different sizes, depending on the specification of particles desired for the product and the end use of the glass. The final particle sizes range from fine glasses (used as pozzolanic materials), to gravel (up to 20mm), demonstrating the flexibility in application for glass used as aggregate.
Mix Design:
The concrete mix is made with:
- Concrete: Ordinary Portland Cement (OPC) or a blended cement.
- Recycled Glass Aggregate: Used as a partial- or complete-replacement for either natural fine or coarse aggregate. In concrete applications, the glass aggregate ratios will range, but are typically somewhere between 10% and 40% by volume. The proportion of portions versus volume must provide balance for the workability, strength and durability requirements for the concrete.
- Supplementary Cementitious Materials (SCM’s): Fly ash, silica fume or ground granulated blast-furnace slag or other materials are sometimes added to further improve durability, reduce permeability or to avoid the issue of Alkali-silica reaction (ASR) of glass aggregate. It can be added generally, 10-30% weight of cement or equivalent.
- Water: Water-cement ratios should be optimized (generally are between 0.4 and 0.5) for optimum hydration, not for shrinkage of hardened concrete.
- Admixtures: Admixtures would include chemical additives, such as superplasticizer for workability, retarder to control set times, and shrinkage-reducers to minimize cracking.
Mixing and Casting:
Fresh concrete consists of a mixture of the following components: dry (cement, SCMs, and glass aggregates) and wet (water/additions). The dry ingredients are mixed together to create a uniform distribution of glass particles (to minimize segregation and ensure mechanical performance), and then water and any needed additions are added and mixed until the fresh concrete is ready to be cast into molds or forms. Depending on placement, vibration is applied to eliminate air pockets and achieve needed compaction.
Curing:
Curing is very important when considering the performance and durability of the concrete, and it is best practice to employ standard curing conditions (e.g., moist curing for 7 days). Inadequate or improper curing, especially when used alongside specific pozzolanic materials, can significantly reduce the concrete’s resistance to issues like alkali-silica reaction (ASR). Therefore, effective curing is essential not only for strength development but also for minimizing potential durability concerns.
Performance Considerations:
- Alkali-silica reaction: Supplementary cementing materials (SCMs) are necessary to mitigate the alkaline aqueous conditions that make ASR possible (i.e., a reaction between the alkalis in the cement and the silica in glass) that will create expansion and cracking.
- Mechanical properties: the glass aggregate influences compressive strength, flexural strength, and workability depending on the size of the glass aggregate particles, their shape and proportions in the glass aggregate in the concrete mixture.
- Aesthetic qualities: They depend on colour or opacity of the glass, it may also be used for decorative finishes such as exposed aggregate or polished concrete.
This technical overview has addressed both composition parameters, as well as process parameters to optimize both performance and durability for the incorporation of recycled glass in concrete.
How is Glass Used in Concrete?
Glass is being used more and more in concrete as a sustainable alternative to traditional aggregates, whether finely ground powder or larger crushed pieces. Using recycled glass in concrete not only reduces landfill disposal but also saves non-renewable resources.
Glass can be used as fine or coarse aggregate in concrete, or as a pozzolanic additive when ground finely. One consideration would be to minimize the possibility for alkali-silica reaction since glass contains silica, which may react with the alkalis in cement to potentially expand and crack the concrete, leading to durability issues. Because of the ASR, it is perfectly acceptable to use other supplementary cementitious materials (SCM) in the concrete mix to help reduce the likelihood of ASR such as fly ash and slag.
If properly controlled, glass concrete can combat environmental sustainability while creating unique visual opportunities that can produce decorative finishes that use the reflective qualities of glass particles fused in the concrete.
Properties of Glass Concrete
Glass concrete has many unique characteristics that make it different from typical concrete:
Visual Appeal: The colored or clear glass elements can yield various visually attractive outcomes, making it easy to use an excellent decorative surface.
Compressive Strength: If engineered correctly, glass concrete can be produced to have compressive strengths similar to traditional mixes.
Durability: If glass concrete is designed correctly with tailored admixtures and particle sizes, then it should have good resistance to chemical attack and weathering.
Thermal Efficiency: The thermal mass values and conductivity can also be altered using glass aggregates, adding performance enhancements for energy efficiency in buildings.
Environmental Responsibility: Using recycled glass keeps materials out of the landfill and has a lower carbon footprint/additional impact on the environment through construction projects.
Pros and Cons of Glass Concrete
Pros of Glass Concrete
- Uses recycled glass that diverts waste from landfills and supports sustainability.
- Creates an architectural landscape with colourful and decorative finishes.
- If designed well it can improve the durability and chemical resistance.
- It may have improved thermal performance that supports energy efficiency. Support sustainable building.
Cons of Glass Concrete
- There is a risk of alkali-silica reaction (ASR) and cracking if not mitigated.
- May require special admixtures or supplementary materials.
- Usually, it is more costly than conventional concrete.
- Quality and supply of recycled glass may fluctuate, which may lead to poor uniformity in concrete.
Applications of Glass Concrete in Construction
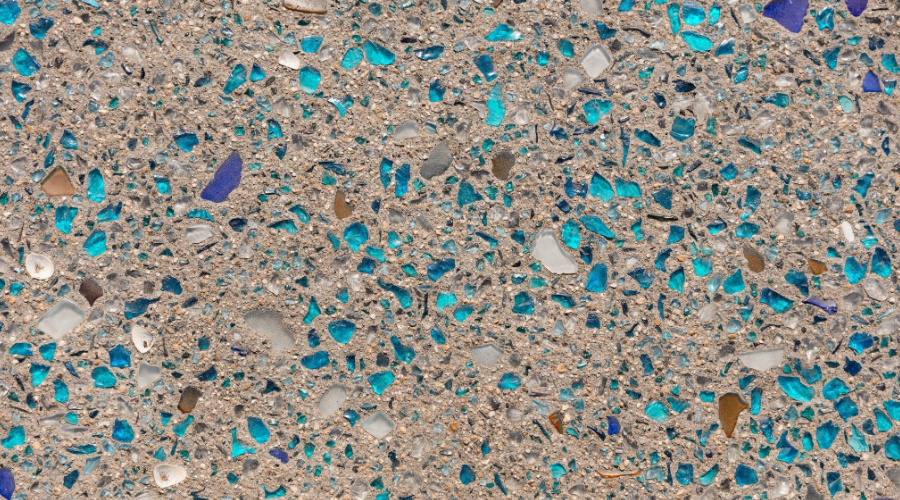
The use of glass concrete is being used more and more in many areas of the construction industry, including:
- Architectural Facades: Their use provides a stunning appearance to building exteriors and curtain walls.
- Flooring and Paving: Glass concrete is widely used in decorative flooring, sidewalks, plazas and so on.
- Precast Elements: It is used to produce tiles, panels and countertops.
- Landscaping: To make features, retaining walls and landscape benches.
- Structural Components: In fewer cases, where it creates a load-bearing wall or column, if proper engineering controls and processes are in place.
Conclusion
Glass concrete offers sustainability and innovation in construction. Glass as an aggregate material performs triple duty: it helps mitigate environmental concerns and expands possibilities for aspiring architects in terms of their creativity and for builders in terms of functionality. Glass concrete will take a key role in our future sustainable, high-performance buildings as we continue to improve our understanding of mix design and production techniques.
Frequently Asked Questions (FAQs)
Yes, when properly engineered, glass concrete can be used for structural components. However, careful mix design and quality control are essential to ensure long-term performance and safety.
Glass concrete utilizes recycled glass, reducing landfill waste and the demand for natural aggregates, thereby supporting sustainable construction practices.
The primary challenge is the risk of alkali-silica reaction (ASR), which can compromise durability. This can be mitigated through the use of supplementary cementitious materials and proper mix design.
Yes, colored glass is often used to enhance the aesthetic appeal of decorative concrete surfaces.
It is widely used in architectural facades, decorative flooring, precast elements, and landscaping features.