Lean concrete is an economical mix that contains less cement and more coarse aggregates. It is most commonly used as a stable, level filler beneath structures, roads, and slabs. Lean concrete also serves as a protective barrier between structural concrete and moisture or harmful chemicals present in the soil. With its wide range of applications in construction, site development, and infrastructure projects, lean concrete is valued for its quick curing time, cost-effectiveness, and durability, making it a popular choice among builders and contractors.
What is Lean Concrete?
Lean concrete is a mix where the cement amount is much lower than that of water and aggregate. A higher aggregate-to-cement ratio makes the mix “leaner.” This results in less binding paste for each unit of aggregate. Common lean concrete mix ratios are approximately 1:4:8 or 1:5:10 (cement:sand:aggregate).
Cement usually constitutes under 10% of the total mix. Although its strength is lower than structural concrete (5 MPa to 10 MPa), it performs well for non-structural applications such as sub-base layers for foundations, floors, and roads. Its primary function is to provide a clean, level, and moisture-resistant base, protecting structural concrete from direct contact with soil and enhancing long-term durability.
Components of Lean Concrete
Component | Their Role in The Mix | M5 Grade | M7.5 Grade | M10 Grade |
Cement | Binding material (reduced quantity) | 1 part | 1 part | 1 part |
Fine Aggregates (Sand) | Fills voids, provides workability | 5 parts | 4 parts | 3 parts |
Coarse Aggregates | Main filler (gravel/crushed stone) | 10 parts | 8 parts | 6 parts |
Water | Hydration and workability | As required | As required | As required |
Properties of Lean Concrete
The properties of lean concrete are as follows:
1. Low Cement Content
Lean concrete usually has a cement content of less than 10% by weight. Low cost and lower cement usage, lean concrete is an economical choice when using large volumes of concrete.
2. High Aggregate Content
Contains a higher percentage of coarse and fine aggregates than compared with cement. Boosts the volume and stability of the concrete mix. This helps it fill voids with greater effectiveness and spread evenly on the surface.
3. High Workability
Lean concrete mix is very workable and flows smoothly into place. It needs little handling and works well for filling high or uneven patches. It’s also great as a base layer.
4. Low Strength
Compressive strength ranges from 5 MPa (M5) to 10 MPa (M10). Not good for structural applications but great for a stable base or filler.
5. Low water-cement ratio
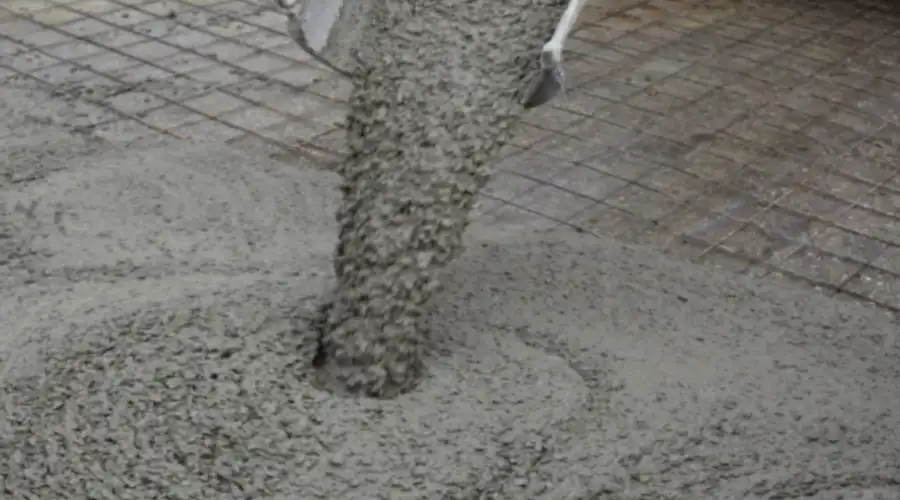
Water-cement ratios are normally higher than structural concrete but controlled to prevent excessive bleeding and segregation. Workability achieved without compromising the integrity of the lean concrete mix.
6. Durability
Not designed to withstand extremes in environmental conditions, or chemical attack. Intended for temporary or protected use, such as sub-bases or blinding layers.
7. Economic
Lower cement content, plus using local aggregates, makes it an attractive option for large-scale groundwork.
8. Shrinkage and Cracking
Generally it has lower cement content, this reduces the potential of shrinkage cracking and thermal cracking when compared to the richer mixes.
9. Placement
Typically can be placed and compacted with little effort, and often without sophisticated machines.
10. Environmentally Sensitive
Environmental Impact- since lower cement content can significantly reduce the carbon footprint and impact of construction activities.
Uses of Lean Concrete in Construction
Lean concrete appears in many applications, including:
- Sub-base for Foundations: A lean concrete gives a flat, solid bed for raft slabs, single pads, and footing blocks so the whole frame sits steady.
- Protection Layer: This thin layer serves as a protective barrier, preventing moisture from the ground from seeping into the main concrete pour and safeguarding the fresh concrete against sulfates and other harmful chemicals.
- Pavement Base: Usually placed under roads or shop floors, it boosts strength, resists cracking, and helps the surface last far longer than normal.
- Filling Voids: Lean concrete quickly levels out hollows, pockets, or rough spots in the subgrade, making the base even and reliable before heavier pours.
Benefits of Lean Concrete
The key advantages of lean concrete are as follows:
- Cost Efficiency: A lower cement mix trims material bills, keeping spending in check.
- Material Conservation: Using less cement saves resources and eases supply chain pressure.
- Foundation Durability: The mix protects against moisture and soil chemicals that harm standard mixes.
- Simplified Application: Lean concrete flows freely, levels itself, and cuts back on finisher’s hours.
Method of Sustainable Construction: Cutting cement demand reduces carbon emissions and lessens project impact.
Preparation and Placement of Lean Concrete
1. Material Selection & Proportioning
- Cement, sand, graded stone, and potable water are required.
- Standard mix: 1:4:8 (cement:sand:aggregate) by volume, or as specified by the job.
2. Batching
- Weigh all materials accurately, using a weighing balance.
- Strict tolerances: cement ±4%; aggregates ±2%; water ±1%.
3. Mixing
- Add the dry materials to a mixer. Then, add water and any admixtures needed. Blend the concrete until its color and texture are even. It should be free from lumps.
- Although workability may be improved by using a higher water-cement ratio, practices should be in place to control segregation.
4. Quality Control
- Perform trial mixes to confirm strength (≥7 MPa at 7 days).
- Inspect for uniformity and adjust water or admixtures as needed.
5. Subgrade Preparation
- Subgrade compacted and graded to the required profile, moist and firm.
- Soft spots fixed prior to pouring.
6. Placing
- Concrete is transported from the batching plant by manual, chutes, conveyors, or pumping as per the convenience and site conditions.
- Concrete is evenly spread to the required thickness and shape, by hand or machine.
7. Compaction
- Compact immediately after placement with rollers/vibrators.
- Focus on joints, edges, and obstructions.
- Achieve at least 97% of trial section density (95% at edges).
8. Finishing & Curing
- Repair surface defects; start curing with water spray or compounds to prevent moisture loss.
- Cure lean concrete for at least 7 days. Then, place the main or structural concrete layer.
This streamlined process ensures lean concrete is produced and placed efficiently and to specification.
How Lean Concrete Differs from Regular Concrete
Feature | Lean Concrete | Regular (Standard/Rich) Concrete |
Cement Content | Less than 10% of the total mix | 10–15% of the total mix for Standard concrete and more than 15% of the total mix for rich concrete. |
Aggregate Content | High | Moderate to low |
Strength | Low (5–10 MPa) | Moderate to high (15 to 30 MPa and more than that) |
Workability | High | Moderate |
Main Use | Sub-base, leveling, protection | Load-bearing elements, foundation |
Cost | Lower | Higher |
Lean concrete is not strong enough for load-bearing or structural use. However, it works well for sub-bases and protective layers.
Conclusion
In conclusion, lean concrete plays a vital supporting role in modern construction by providing a reliable, cost-effective base for structural elements. Its ability to improve ground stability, protect structural concrete from environmental factors, and offer a quick, durable solution makes it an essential material in site preparation and infrastructure works.
Whether used beneath pavements, foundations, or roadways, lean concrete ensures long-term performance and efficiency, making it a trusted choice for engineers, builders, and contractors alike.