Prefabricated buildings in India had a market size of USD 15.07 billion in 2025. In the previous year, 2024, the market value was 13.83 billion. There is a rise each year. The growth of this industry can be measured with predictions saying that the growth is expected to reach USD 23.13 billion by 2030, at a CAGR of 8.95% during the forecast period (2025-2030).
As the Indian government supports urbanisation and industrial developments, the growth of PBE systems in India is notable and promising. This method is used to construct structures like community halls, large warehouses, and stadiums across various sectors. In this Brick & Bolt article, we will explore the key components, applications, advantages, and other essential things about PEB structures in detail.
What is PEB?
A pre-engineered Building (PEB) is a prefabricated Construction that can be delivered to the site for erection. These structures are very high in strength and resilience. These are most commonly used for constructing buildings for industrial, commercial, and other institutional applications.
PEBs are easily customisable to the project requirement. It can adapt to any design or style and is applicable to a factory, warehouse, or office environment. It accelerates the construction process and allows businesses to start operations immediately. Overall, PEB structures have many advantages for many kinds of construction projects.
Components of the PEB Building
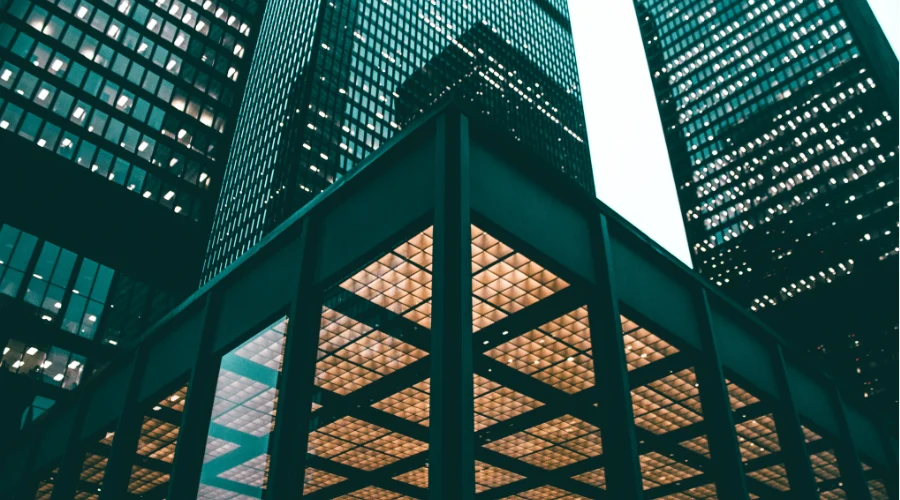
Different steel parts are combined to create pre-engineered building structures to acquire strength, support, and protection. These include:
Primary Members (Main Structural Parts)
These are the key load-bearing elements of a structure. They include columns, rafters, and crane beams, which form the framework. Built-up I-shaped steel members, trusses, and castellated beams to provide strength and stability to the overall structure.
Secondary Members (Supporting Components)
Common secondary members include purlins (often cold-formed in “Z” or “C” shapes), bracings, tie rods, and angle bracings. High-tensile bolts and washers are used to hold these members firmly together.
Roofing & Wall Panels
These elements form the external covering of the structure. Materials like tin shades, glass curtain walls, roll-formed steel sheets, and roof or vertical cladding panels are commonly used. Skylight sheets are also installed to allow natural light inside the building.
Additional Accessories
Accessories include ventilators, louvers, downspouts, insulation materials, mezzanine floors, bolts, and other essential fittings that complete the structure.
Advantages of PEB Building
The several benefits of PEB buildings are as follows:
- While the foundation is built on-site, the steel parts are made in factories. Since assembly takes less time, the building is completed quickly.
- Most work is done in factories, so fewer workers are required at the construction site.
- Using less material and fewer workers helps reduce overall Prefabricated construction costs.
- Steel parts are designed using software and made by machines, allowing custom shapes without compromise.
- Since bolted connections are used, the building can be easily expanded in length.
- Steel is shielded from rust and chemicals by special coatings, and any damage is quickly fixed.
- Steel is more effectively resistant to earthquakes than concrete due to its lightweight and flexible properties.
Disadvantages of PEB Building
Several limitations for using PEB buildings are as follows:
- If not maintained well, steel frames can rust over time. Special coatings are needed to protect them.
- Steel conducts heat, making the building less comfortable in hot weather.
- Steel heats up fast in a fire, which can weaken the structure.
Application of PEB Building
Several applications of PEB buildings are discussed here:
- Factories use PEB structures to create large workspaces for making products.
- Warehouses need big, open spaces to store goods and materials safely.
- A workshop is a space that can be built using the PEB method for repair work, manufacturing, or small-scale production.
- These buildings are used for a group of events, meetings, and social gatherings, which accommodate a large number of people at one time.
- Businesses use PEB structures as showrooms to display their products, like cars, furniture, or electronics.
- PEB buildings can also serve as cold storage areas that help in storing fruits, vegetables, and dairy products at low temperatures.
- These buildings are also used as stadiums that provide large seating areas for sports and events.
- PEB sheds protect vehicles from the sun and rain. They can cover large areas and shelter more vehicles.
- PEB structures give shelter to passengers at railway stations.
- PEB buildings are used in airports for waiting areas, cargo storage, and hangars.
PEB Building Construction Process
Step 1:
Design of PEB Structure
Engineers design and make steel frames in a factory. They use special software to make sure there are no mistakes. This design is very important for the PEB structure.
Step 2:
Construction of Foundation
Workers clean the site and build concrete foundations. PEB structures usually need shallow foundations because they are lightweight.
In coastal areas, they use pile foundations, but these are not as deep as in regular buildings. A flat concrete slab (PCC) is placed below the pedestal to stop direct contact with soil. The columns are bolted to the pedestal.
Step 3:
Erection of Steel Frames
The steel used for constructing a structure could be different based on the type of building. Thin steel (0.9 mm to 1.2 mm) is required for small buildings, and bigger buildings require thick steel (4 mm to 50 mm).
Labourers bolt beams and columns of steel together. Steel is also used for roofing in single-storey buildings and for both floors and roofs in multi-storey buildings.
Step 4:
Construction of Walls
Workers construct walls with various materials such as fiber cement panels, insulated steel, aluminium panels, bricks, or stone. Insulated steel panels are popular due to their strength and stability.
Construction of Roof
In a PEB building, the roof is built by first fixing the main steel frame with rafters and columns. Then, purlins are added to support roof sheets made of lightweight steel. Finally, accessories like gutters, ventilators, and insulation are installed for protection and comfort.
Key Materials Used in PEB Construction
The key material used to build pre-engineered buildings is steel. Steel is the most highly recycled substance globally. Steel is predominantly manufactured using recycled products and can be reused for multiple applications without processing. Steel structures are also recyclable at their life’s end and recycled once again to minimise landfills. Moreover, steel is cost-effective, reducing utility bills.
Why Steel is Chosen for Building Pre-Engineered Buildings?
1. Faster Construction Time
Steel components are made in a factory, ensuring on-time production without weather delays. Unlike field construction, factory-made steel offers better control. Building Information Modeling (BIM) helps designers and steel contractors work together efficiently. BIM technology saves both time and money in the construction process. Steel allows for fast erection in all seasons without reducing quality.
2. Lower Project Costs
Steel frames are the most cost-effective option for PEB structures. Studies show that steel framing, including decking and fire protection, costs 5% to 7% less than concrete framing.
3. Durability
Steel is much stronger than other materials. It typically has a yield stress of 50,000 pounds per square inch, making it highly durable and reducing maintenance costs.
Conclusion
In a nutshell, PEB structures serve their purpose for various sectors in India. With India’s rapidly growing industries and construction technology, these PEBs are a popular choice for building many functional structures.
This allows for a speedy construction process, and they can be tailored to serve specific requirements, whether it is a warehouse, cold storage, or any other office setting. You can call our expert team members if you have queries related to PEBs.