In modern construction, the use of prefabricated components has increased tremendously. Their popularity has been widely recognised all over the world in recent years. As they are manufactured in a controlled environment with specific conditions off-site, they allow for efficient assembly and installation processes on-site. This article throws light on the prefabrication of components, their types, common applications, and methods. So keep reading to gain insightful knowledge about this technology in the construction sector.
What is Prefabrication in Construction?
Construction involves prefabrication, which means that the actual key elements, such as walls, floors, and roofs, are built inside a controlled factory or manufacturing facility. This process is also known as prefab. Before being shipped to the final installation location, these parts may be assembled entirely or in part at a factory.
Overview of Prefabrication in Construction
Prefabricated structures are built off-site, and as such, are widely known to be cost-effective, speed up the construction process, and have the potential for reusability. They have diverse applications ranging from temporary buildings to office structures, medical centres, schools, apartments, and individual houses.
With their efficient manufacturing techniques, they surpass the traditional on-site construction methods. A production line method is made possible by the fact that many structures contain similar or identical portions in their floors, walls, and roofs. This improves efficiency by streamlining activities and making it simpler to analyse and enhance the overall procedure.
Types of Prefabrication in Construction
A wide range of components, including steel, concrete, and other material systems, are included in prefabricated construction methodologies. Typical prefab systems include:
Panelised Wood Framing:
Long timber frames that have been laminated and coated with plywood or roofing material make up panelised wood framing systems. They are frequently utilised for building roofs.
Advantages
- Cost-effective and easy to transport.
- Quick assembly and flexible design.
Disadvantages
- Less durable than other materials.
- Susceptible to moisture damage over time.
Sandwich Panels:
As the name suggests, sandwich panels are made up of two layers of materials with an insulating core between them. The exterior layers may be made of concrete, plywood, or stainless steel, while the insulating layer may be made of rubber, foam, or paper.
Advantages
- Excellent insulation properties, improving energy efficiency.
- Lightweight and easy to install.
Disadvantages
- May have limited aesthetic appeal.
- Can be expensive depending on material choices.
Steel Framing:
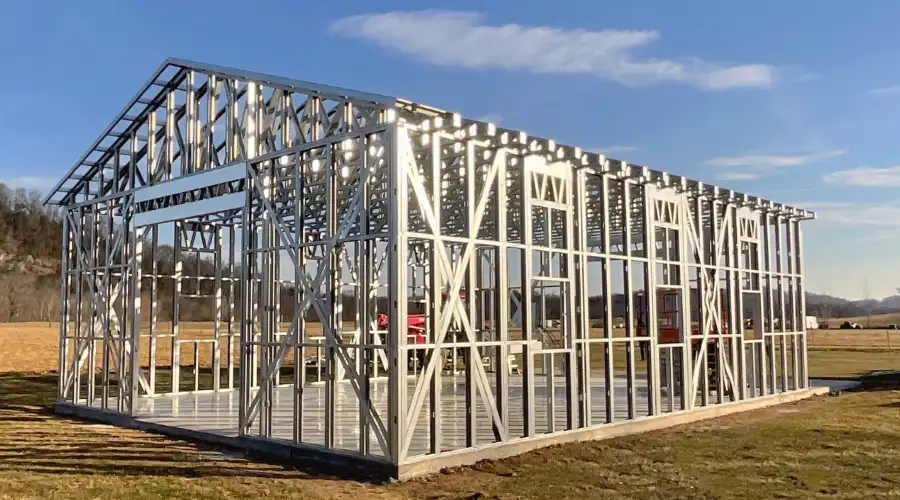
With sturdy and long-lasting properties, steel framing systems offer a solid structural foundation for building construction.
Advantages
- Strong and durable, with resistance to fire and pests.
- Requires less maintenance.
Disadvantages
- High initial cost.
- Susceptible to corrosion if not properly treated.
Timber Framing:
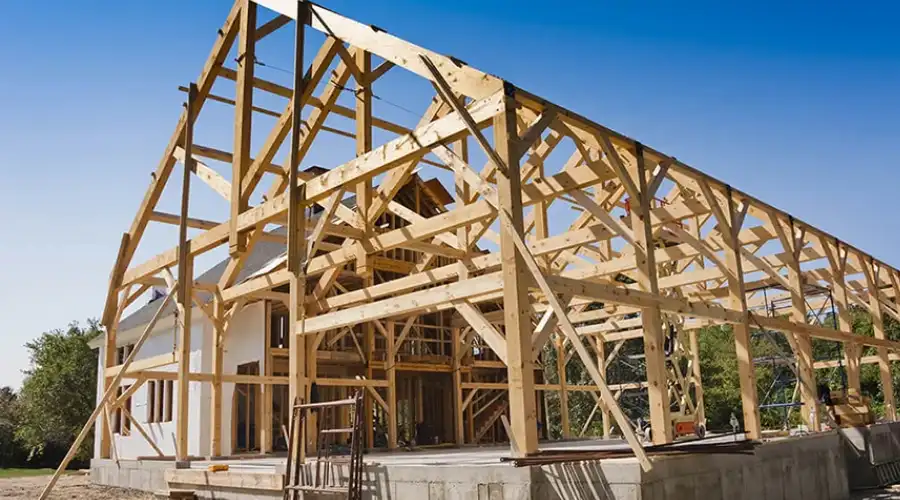
Although this technique is less popular in India, timber panels are used to build timber homes.
Advantages
- Environmentally friendly and renewable.
- Provides natural insulation and aesthetic warmth.
Disadvantages
- Can be more prone to rot and pests.
- Limited availability in some regions, like India.
Concrete Systems:
Concrete elements provide time savings and versatility in prefabricated buildings. Concrete is strong and adds to the structure’s visual appeal despite its weight.
Advantages
- Strong and durable, offering excellent structural integrity.
- Low maintenance and long-lasting.
Disadvantages
- Heavy, making transportation and installation challenging.
- Higher material costs.
Modular Systems:
The components of the structure are made entirely of prefabricated parts; these systems are put together in the desired location. To finish the construction, the components are joined or set after being shipped from off-site factories.
Advantages
- Fast construction with pre-made, fully finished units.
- Minimises site disruptions and labour costs.
Disadvantages
- Limited design flexibility.
- Transporting large modules can be costly and complex.
Benefits of Prefabrication in Construction
Here are the key points on the benefits of prefabrication in commercial projects:
- Reduces labour shortages by speeding up timelines and increasing on-site productivity.
- Cost-effective as components are assembled in factories instead of transporting materials to each site.
- Modular buildings can be completed up to 50% faster than traditional construction, crucial for weather-sensitive projects.
- Factory settings improve quality, reduce delays, and enhance safety.
- Minimises environmental impact by conserving resources, recycling materials, and using fewer fossil fuels.
- Faster construction reduces exposure to theft or damage, helping secure the building sooner.
Common Applications of Prefabrication in Construction
Residential Houses:
While building sub-urban or urban development projects like apartments, individual residences, and villas, builders and investors show more interest in incorporating prefabricated components for building structures. While working on similar projects, prefabricated components help the builders construct the structure within the timeframe and budget. It helps to cut down cost overruns and streamline the projects.
Commercial Buildings:
Prefabrication is also raising an uproar in the commercial construction industry. Prefabricated materials enable developers and contractors to build such structures as commercial buildings, schools, and hospitals much faster and at a cheaper rate.
Infrastructure Development Programs:
Prefabrication works well for large infrastructures, such as roads and bridges. This method allows for faster completion, cost savings, and reduced traffic intermissions.
What are the Steps of Prefabrication?
- Architects and engineers draft comprehensive plans that specify materials and measurements.
- The design determines the selection of materials such as steel, wood, and concrete.
- Since components are manufactured in a facility, accuracy and quality are guaranteed free from weather-related disruptions.
- To guarantee safety and structural integrity, prefabricated parts are put together into bigger portions.
- Parts are delivered to the building site with care.
- Plumbing and electrical systems are installed, and modules are connected.
- Final touches include the addition of windows, doors, paint, and flooring.
- To ensure that the building satisfies requirements, it is subjected to inspections.
- The building is finished and operational.
Conclusion
The prefabricated construction method helps to save project timelines, improve on-site safety, and enhance the durability of structures by providing high-quality building components. Waste reduction, enhanced air quality, greater quality control, and efficient management are further advantages. However, large-scale projects benefit the most from prefabrication.
Prefabricated parts must be delivered to the construction site following a meticulously planned schedule to guarantee efficient development. By doing this, delays are avoided, and extra space is not occupied by items that arrive earlier than required.