Hydrographic element, also known as hydraulic cement, is prepared with water-repelling chemicals as additives. It is best suited for construction projects where physical contact with water is unavoidable, such as spillways, dams, and water-retaining structures.
The primary characteristics of this cement are its high workability and strength, which are mainly unaffected by rain or monsoons. Due to its water-repelling properties and withstanding efficiency in wet conditions, it is designated for marine and underwater construction projects.
This article explains to you the application of hydrographic cement, and it is different from others.
Applications of Hydrographic Cement
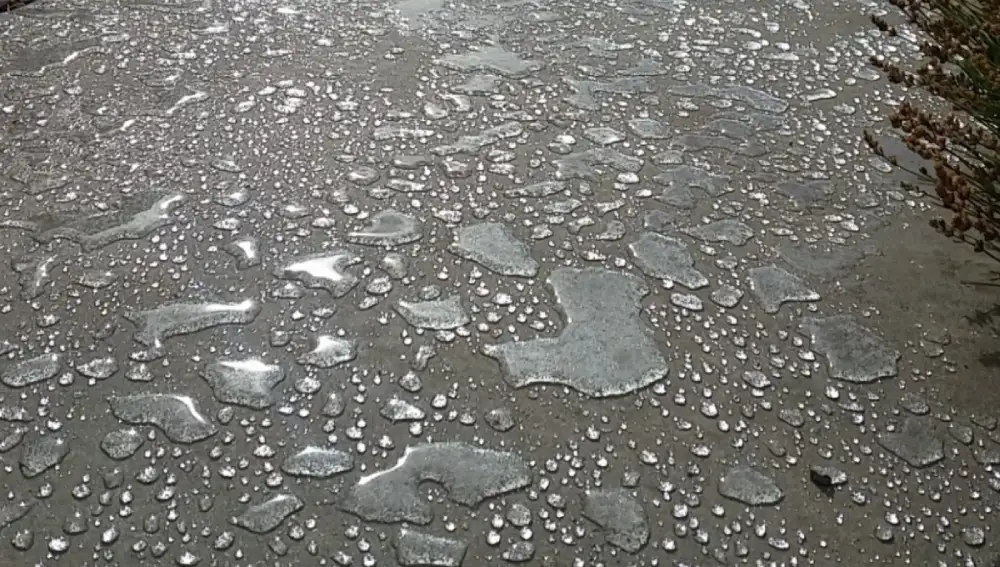
Hydrographic cement is a highly durable and versatile material that has been identified in various construction projects where water exposure is a major concern. Here are some keys where it is efficiently used:
Marine Construction
As mentioned earlier, hydrographic cement has enhanced water-repelling properties as it can set perfectly underwater. It is primarily used in structure designs such as bridge piers, dams, offshore wind turbine bases, seawalls, etc.
It serves consistent reliability and a stable foundation, offering robust protection against erosion and seawater damage.
Swimming Pools
The construction of decorative water features like swimming pools requires a durable and water-resistant base. A hydrographic cement, named for ultimate waterproofing capabilities, ensures leakproof and maintains water-tight integrity.
Building Foundations
Though traditional cement includes various protecting features, it suffers from water infiltration and tends to meet structural damage over time. However, hydrographic cement has excellent water resistance properties, hence protecting the overall structural integrity of buildings.
Waterproofing Basements and Moisture-Prone Structures
The construction structures and basements that are highly volatile to moisture can benefit from hydrographic cement. It seals the basement floors and walls and prevents water seepage therefore, you can protect your buildings from mold and mildew.
Filling Foundation and Cistern Cracks
Fountains and cisterns can be affected by the high water pressure pressing against the walls. This can cause the walls to crack over time, leading to water leakage and contamination.
Hydrographic cement can fill or repair cracks, stop leaks, and prevent further damage.
Benefits of Using Hydrographic Cement
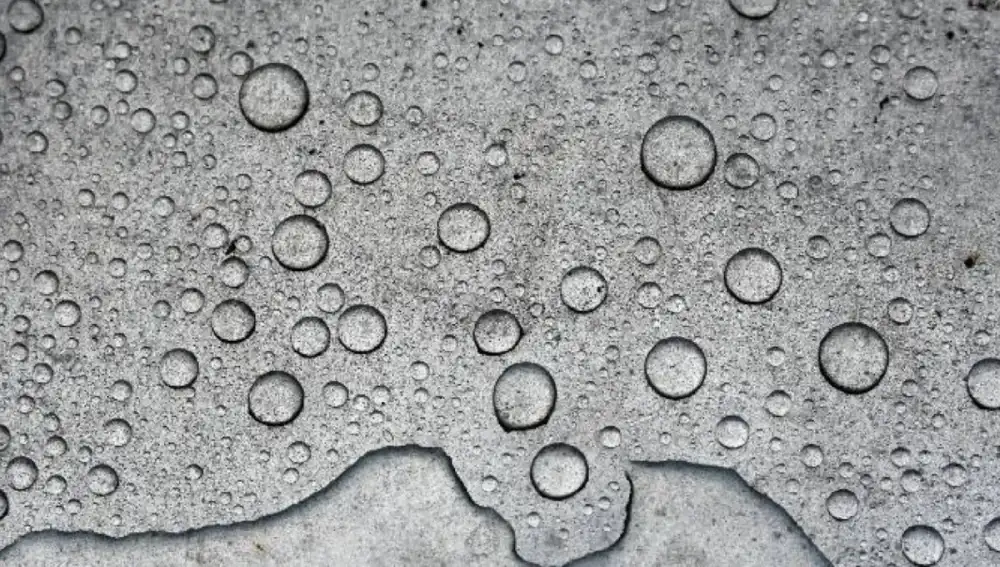
Hydrographic cement offers a plethora of advantages, and it is a preferred choice for construction projects particularly related to water exposure. Its ideal characteristics and performance benefits contribute to its use in different applications. Here are some notable benefits are listed:
Durability
One of the standout features to be highlighted is exceptional durability. It is capable of withstanding chemical attacks, harsh environmental conditions, water pressure, etc. The enhanced durability makes it an ideal choice for water-exposed structures, offers a longer lifespan, and meets with fewer repairs and maintenance.
Faster Setting Times
A rapid setting time is another notable feature here. Unlike traditional cement, it doesn’t take a few days or weeks to fully set. It can be fixed within a few minutes to hours based on the specific formulation. This Cement quick setting time is advantageous when you have a tight deadline and work during monsoon seasons.
Improved Workability in Wet Environments
Hydrographic cement is specifically established to perform construction projects in a wet environment. Its required formulation is prepared, placed, and cured underwater, there is no chance of delay or complications caused. This feature improves efficiency and reduces the time consumption of overall construction projects without any compromises in quality and performance.
Reduced Risk of Voids and Defects
With its extended durability, structures can be free from any kind of risks like voids and defects during the curing time. It can set quickly and reduces the chances of forming air pockets and inconsistencies. Because it is pre-mixed, the particle sizes are very fine resulting in filling the gaps and cavities more effectively. Overall, the building structure seems uniform and solid.
Potential Cost Saving in the Long Run
Hydrographic cement may cost more than the traditional cement. But it keeps you away from frequent repair, replacement, and maintenance costs over the long term. Additionally, the project timeline is shorter, leading to reduced labor costs and improved workability.
Hydrographic Cement vs Hydrophobic Cement
Aspects | Hydrographic Cement | Hydrophobic Cement |
What it is | Set quickly and harden when exposed to water or high moisture areas. | It repels the water molecules and prevents moisture absorption. |
Setting time | Rapid setting time takes fewer minutes to hours. | Standard setting time may take a few days to weeks. |
Workability | Improved performance in wet environments. | Offers standard workability |
Durability | Enhanced durability and reliability in water-exposed areas. | Maintains high durability in moisture areas. |
Primary Use | Wet areas and underwater construction | Structures that are highly exposed to moisture |
Maintenance | Lower maintenance required | Lower maintenance required |
Cost | Higher initial cost | Potentially lower cost, similar to traditional cement. |
Conclusion
The construction work in the water related areas is quite typical as it needs strong support to balance. Such balance here is hydrographic cement and is explained in detail above. Its usage and performance in wet conditions is simply amazing, while there is no frequent repair or maintenance required.